Starting Self Storage as a Business: Your Complete Guide
Thinking about getting into the self storage business? It's a solid move. At its core, you're providing secure, rentable space for people and businesses, creating a steady monthly income from a physical property. But success isn't just about putting up a few units; it comes down to a great location, smart management, and really getting to grips with what your customers need.
Is Self Storage a Good Business Venture?
Diving into the self storage market is a big decision, and you need to understand the numbers before you jump in. This isn't just about renting out empty boxes. It's a dynamic property business with its own economic quirks, running costs, and customer types. The real appeal is its simple revenue model and how well it holds up when the economy gets shaky. When times are good, people buy more stuff and need somewhere to put it. When things get tough, life changes like downsizing or moving create just as much, if not more, demand for storage.
The industry is in great shape. The UK self storage market recently hit an impressive turnover of £1.2 billion. This is backed by around 2,915 facilities across the country, showing just how established and widespread the business is. If you want to dig deeper, you can learn more about the boom in container storage facilities from Cleveland Containers.
To give you a clearer picture, here's a quick look at the UK self storage market right now.
UK Self Storage Market at a Glance
Metric | Figure |
---|---|
Annual Industry Turnover | £1.2 Billion |
Total Number of Facilities | 2,915 |
Total Rentable Space | 60.5 Million sq ft |
Container-Based Sites | 1,135 |
Average Net Rental Rate | £26.49 per sq ft/year |
These figures paint a picture of a healthy, growing industry. It’s not just surviving; it’s thriving, with plenty of room for new players who get the formula right.
Revenue Streams and Operational Costs
Your main income will obviously be the monthly rent from the units. But the savviest facilities don't stop there. Ancillary sales are where you can really boost your profits.
Think about adding these to your offering:
- Retail Sales: Selling essentials like locks, boxes, and packing tape on-site is a no-brainer.
- Insurance: Offering tenant insurance gives your customers peace of mind and earns you a nice commission.
- Late Fees: Nobody aims for them, but late fees are a reality of the business and they do add to the bottom line.
- Van Hire: Partnering with a rental firm or having your own branded van is another service that generates income and makes your customers' lives easier.
On the other side of the coin, you have your running costs, which are thankfully quite predictable. You'll be looking at property taxes, staff wages, insurance, utilities, marketing, and management software. A well-managed facility can expect to see operating margins between 40% and 60%, which makes self storage a very attractive option compared to other types of commercial property.
Choosing Your Business Model
Not all self storage sites are the same. The model you choose will depend heavily on your budget, vision, and where you plan to build. In the UK, two main formats dominate the scene, and each has its own pros and cons.
Traditional Multi-Storey Facilities
This is the classic image of self storage: a large building with internal corridors, climate-controlled units, and lifts to get between floors. They’re usually found in cities or busy suburbs and appeal to a wide range of customers, but the cost of land and construction is significantly higher.
Container-Based Storage
This model has absolutely exploded in popularity, especially in semi-rural spots where land is cheaper. It’s all about converting shipping containers into secure, drive-up units. The setup is quicker, more flexible, and requires less cash upfront. It’s a huge hit with customers who value easy access over extras like climate control. In fact, 1,135 of the UK's facilities are now container sites, which tells you everything you need to know about their rise.
The secret is to match the type of facility to your local market and your wallet. A container site could be perfect for an area with lots of tradespeople needing to store tools and equipment. A multi-storey building, on the other hand, is ideal near new housing estates or areas with a lot of renters.
Understanding Your Customer Base
Finally, if you want your self storage business to succeed, you need to know who you’re serving. Your customer base is far more varied than you might think.
- Residential Movers: These are your bread and butter. People moving house, downsizing, or doing a big renovation will always need storage.
- Small Businesses: E-commerce sellers storing stock, builders securing their tools, and offices archiving documents are a crucial, long-term source of revenue.
- Students: The need for storage over the summer holidays provides a reliable, seasonal spike in business.
- Life Events: People going through big life changes—like divorce, inheritance, or moving abroad—often need a temporary space for their belongings.
Getting your head around these different needs is the first step toward building a business that doesn't just get by, but genuinely flourishes.
Finding the Perfect Location for Your Facility
The old estate agent mantra of 'location, location, location' is more than a cliché in the self-storage world; it's the absolute foundation of your success. I’ve seen it time and again: a brilliant facility in the wrong place will struggle, while an average one in a prime spot can absolutely thrive. Pinpointing that perfect site means going far beyond a simple map search. You have to dig into the data that reveals real, unmet demand.
Think of yourself as a local detective, hunting for signs of growth and transition within a community. What you're really looking for are areas where people are actively in need of storage. Key indicators include rising population figures, high housing turnover, and a growing number of small businesses. These factors signal a dynamic area where people and companies are constantly experiencing life changes—the very changes that create a need for extra space.
Analysing Regional and Local Demand
First, let's look at the big picture. Market data shows that growth in the UK self-storage sector isn't happening uniformly across the country. It’s patchy, and you need to know where the hotspots are.
Regionally, the market shows uneven growth that lines up with population density and economic activity. The South East and North West of England are leading the charge in inventory expansions, with projected increases of 6.3% and 4.9%, respectively. Other strong contenders include the West Midlands (3.2%), East Midlands (2.8%), and the South West (2.1%). On the flip side, regions like London (1.2%) and Scotland (0.7%) are seeing much more modest growth.
This high-level view helps you narrow down promising counties or regions, but the real gold is in the local details. That’s where you’ll find your opportunity.
Start drilling down with these local data points:
- Population Density and Growth: Get your hands on data from the local council and the Office for National Statistics (ONS). A growing population, especially one with a high concentration of renters or people in smaller homes, is a massive green flag.
- Housing Market Activity: High rates of house sales and new developments mean people are on the move. And movers are, without a doubt, one of the biggest customer segments for self-storage.
- Business Density: Check local business directories and see what’s happening on the ground. A high number of small businesses, particularly e-commerce sellers or tradespeople, points to strong commercial demand for units.
This infographic gives you a great visual summary of how these key market insights come together.
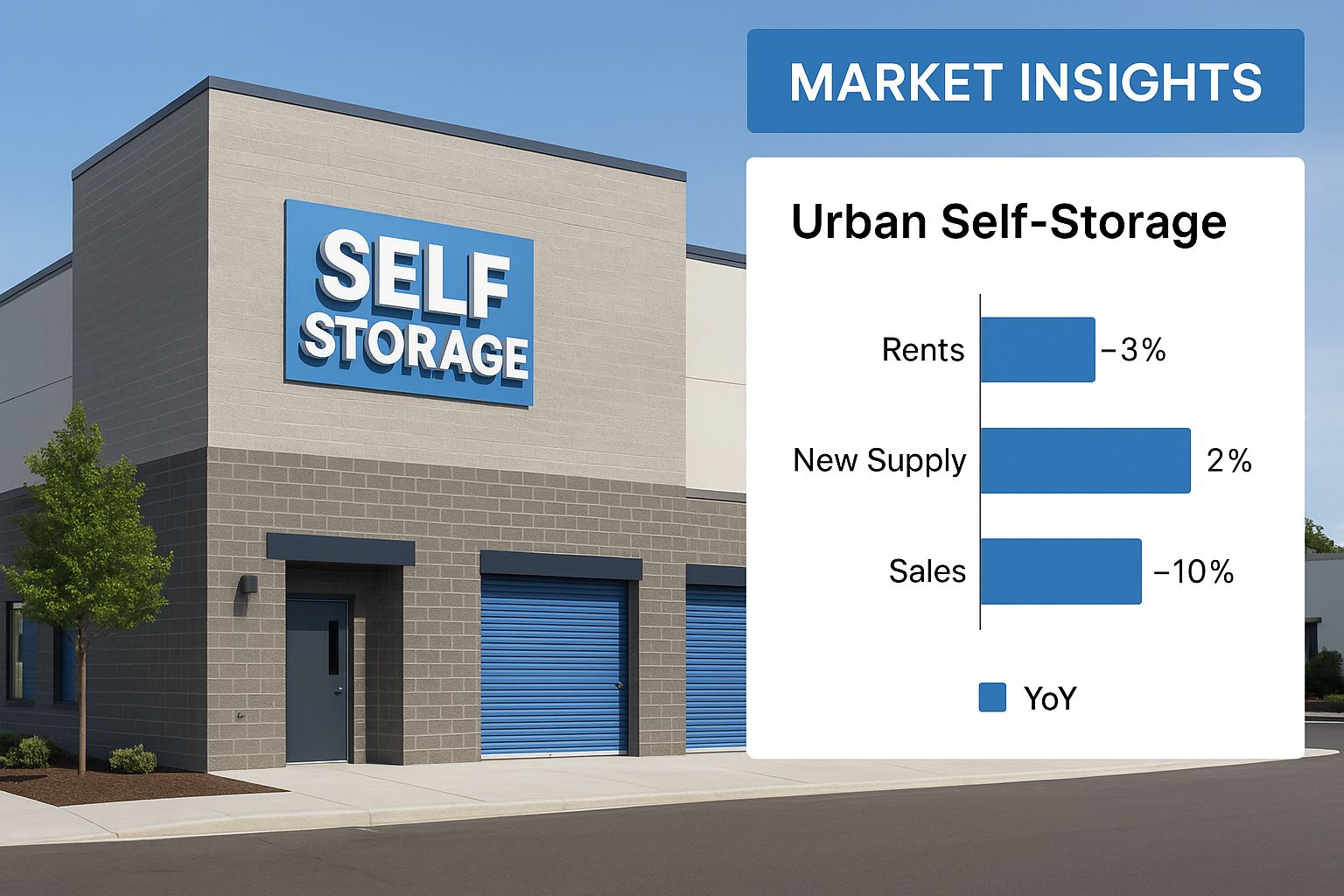
As you can see, it's the combination of population trends, housing data, and a sharp eye on the competition that will lead you to a location with built-in demand.
Sizing Up the Competition
Once you've zeroed in on a promising area, it’s time for some old-fashioned reconnaissance. Don't just check your potential competitors' prices online. You need to get a feel for their business on a much deeper level to find the gaps you can exploit.
Get in your car and visit their sites in person. Is the facility clean and well-maintained? Is access easy and secure? Make a note of their opening hours, the unit sizes they offer, and the general state of the property. A tired-looking competitor with limited hours could be an easy target for a modern, 24/7 access facility.
A critical mistake new owners make is underestimating existing competitors. Just because a facility looks old doesn't mean it isn't full. Always try to gauge their occupancy levels—a full car park during peak hours is a good sign they're doing well, which proves market demand.
Your competitor analysis has to extend online, too. Read their Google reviews carefully. What are customers really complaining about? Common issues often revolve around poor customer service, unexpected price hikes, or security concerns. Every single negative review is a clue, telling you exactly how to build a better service and win their customers over.
Zoning Regulations and Site Practicalities
Finding the perfect plot of land is only half the battle; you also have to be allowed to build on it. Before you get too attached to a site, you must investigate local zoning and planning regulations. Your best bet is to look for land zoned for industrial or commercial use, as these are most likely to get the green light for self-storage development.
Once you’ve found a suitable plot, put it through a practical reality check:
- Visibility: Can your site be easily seen from a major road? High visibility is free marketing, pure and simple.
- Accessibility: How easy is it for customers to get in and out, especially with large vans or lorries? Poor access is a major turn-off.
- Site Layout: Does the plot's shape allow for an efficient layout of buildings and driveways? Awkwardly shaped plots can seriously reduce the number of units you can build, which directly hurts your potential revenue. To learn more, check out this essential guide to building the best self storage units.
Finally, whether you're buying or leasing the land, legal diligence is absolutely crucial. When you’re this close to identifying the perfect location, understanding the ins and outs of negotiating a commercial lease is paramount. This is what secures favourable terms and protects your investment for the long haul.
Navigating Planning, Design, and Construction
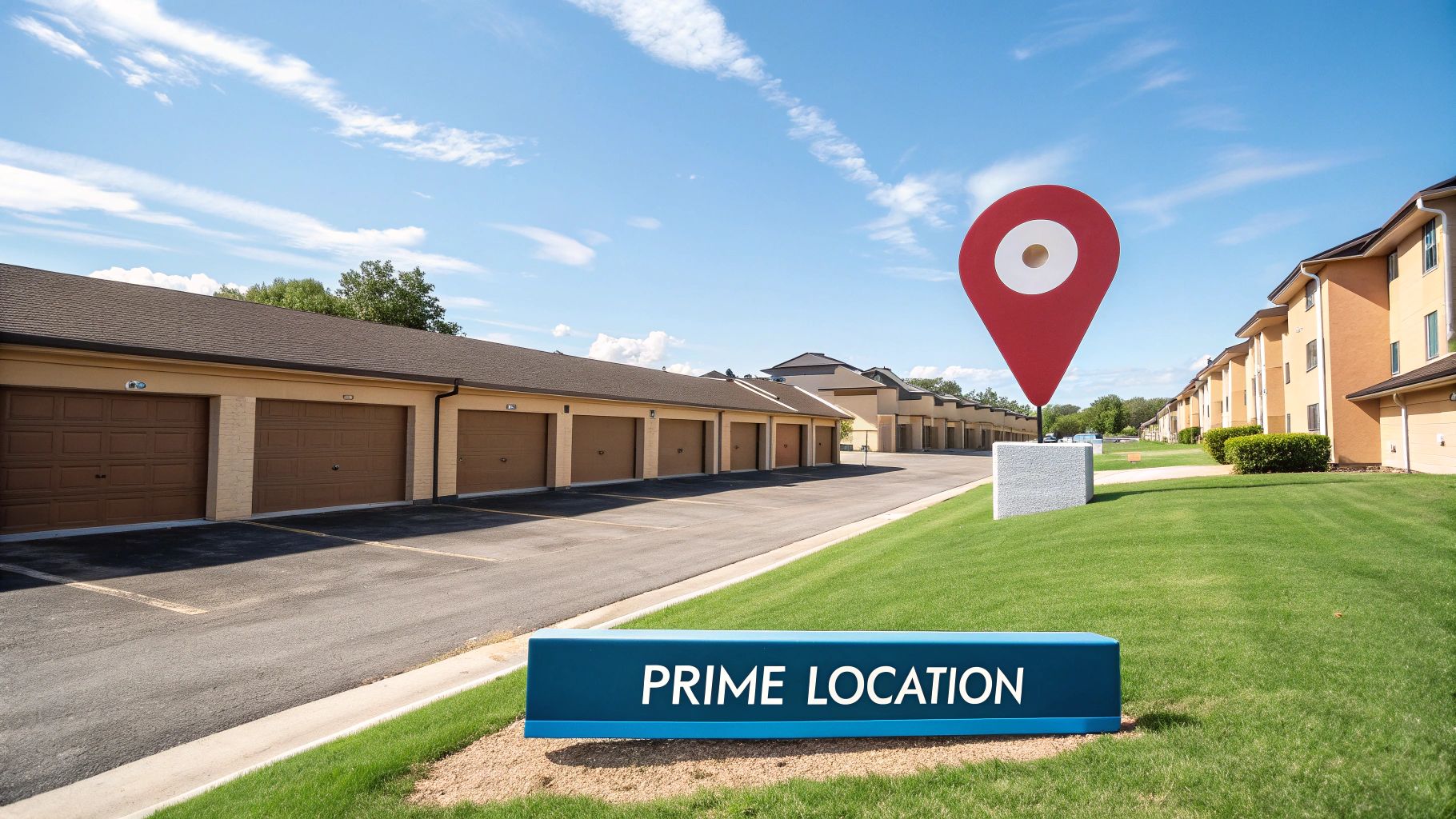
This is where your vision for a self-storage as a business venture starts to take shape. Turning an empty plot of land into a profitable asset is a complex but rewarding journey, involving careful planning, smart design, and diligent construction management. Getting these elements right is non-negotiable for long-term success.
The first major hurdle in the UK is securing planning permission. I know the process can feel daunting, but solid preparation is your greatest ally. At the end of the day, local councils just want to see a well-considered project that benefits the area without causing disruption.
Your application needs to clearly show how your facility will meet local demand, address traffic flow, and fit aesthetically within the surroundings. Working with an architect or a consultant who has experience with local councils can make a huge difference here—they know the specific nuances and requirements that need to be met.
Crafting a Profitable Unit Mix and Layout
Before a single shovel hits the dirt, you need a blueprint for profitability. That starts with designing the perfect unit mix—the variety of unit sizes you'll offer. This isn’t guesswork; it’s a strategic decision that should flow directly from your market research.
For instance, if your site is near a university, you'll likely need more small, locker-style units for students. A facility in a suburban area full of families, on the other hand, will see much higher demand for larger units—think 100 or 150 square feet—to accommodate furniture during a house move.
Your unit mix has to reflect the real needs of your target customers. A solid starting point usually includes:
- Small Units (25-50 sq ft): Perfect for students, renters, or people storing seasonal items.
- Medium Units (75-100 sq ft): Typically the most popular size, ideal for the contents of a one or two-bedroom flat.
- Large Units (150+ sq ft): Suited for families moving house or businesses needing to store inventory.
The site layout is just as crucial. You have to strike a balance between maximising rentable space and providing a seamless customer experience. Wide driveways for removal lorries, clear signage, and logical numbering are essential. A poorly designed layout leads to customer frustration and operational headaches you just don't need. To dig deeper into this, our detailed guide offers valuable insights into self-storage design and innovative layouts for maximum efficiency.
Traditional Builds vs Container Sites
A fundamental choice you’ll face early on is the type of construction. The two main paths offer distinct advantages and disadvantages, heavily influencing your initial investment and your entire operational model.
Traditional Construction
This involves building a permanent, multi-storey structure. It gives you far superior options for climate control and security, which appeals to a broader customer base—especially those storing sensitive items. The trade-off? The upfront cost and construction timeline are significantly greater.
Container-Based Sites
Using modified shipping containers has become an incredibly popular and cost-effective route to market. The speed of deployment is a massive advantage; you can be up and running in a fraction of the time. This model is perfect for sites where drive-up access is a key selling point, particularly for tradespeople and small businesses.
Choosing between these models often comes down to your location and capital. A tight city-centre plot might demand a multi-storey build to maximise its small footprint, whereas a larger, semi-rural site is perfectly suited for a phased container rollout.
Managing Construction and Security Integration
Once you’ve finalised a design, the focus shifts to bringing it to life. Vetting and selecting the right contractors is one of the most important decisions you will make. You need to find builders with proven experience in commercial or industrial projects, and always, always check their references thoroughly.
Throughout the construction phase, keeping a tight grip on your budget is absolutely critical. Unexpected costs are almost inevitable, so having a contingency fund of 10-15% of the total construction budget is a wise safety net. Regular site meetings with your contractor will help keep the project on track and let you address any issues before they escalate.
Finally, integrate security features right from the very beginning. Modern customers expect top-tier security, and this is not an area to cut corners. Your plan must include:
- Perimeter Fencing: A robust, anti-climb fence is your first line of defence.
- Automated Gate Access: Keypad or app-based systems that log every single entry and exit.
- High-Definition CCTV: Comprehensive camera coverage of all driveways, corridors, and entry points.
- Individually Alarmed Units: A premium feature that offers customers ultimate peace of mind and justifies higher rates.
Building these security measures into the initial construction is far more cost-effective than trying to retrofit them later on. It shows customers you’re serious about protecting their belongings from day one.
Funding Your Venture and Crafting Your Business Plan
With a solid location and a clear design in mind, you’ve reached what is arguably the most critical stage: securing the capital to bring your vision to life. This is where your self-storage concept meets the hard reality of finance. A meticulously crafted business plan isn’t just a formality; it's the master key that unlocks the funding you need to break ground.
Think of your business plan as the story of your future success, told with numbers and strategy. Lenders and investors have seen countless proposals. Yours has to stand out by being both ambitious and, more importantly, completely believable. You need to prove that you've not only had a good idea but that you've scrutinised every single detail of making it a profitable reality.
Building a Plan Lenders Want to Read
Forget generic templates. A compelling business plan is tailored to the unique aspects of your project. It needs to clearly articulate the opportunity you’ve found and exactly how you intend to capitalise on it. This document is your primary sales tool for proving your venture is a sound investment.
Your plan should have a few core components:
- Executive Summary: A punchy, powerful overview of the entire plan. Write this last, but always place it first.
- Company Description: Get into the specifics of your legal structure, mission, and the exact services you'll offer—container storage, climate-controlled units, dedicated business spaces, you name it.
- Market Analysis: This is where you present the hard data you’ve gathered. Show them the local demand, population growth, and housing turnover figures. Prove an underserved market exists.
- Competitive Analysis: Don't just list your competitors. Dig into their weaknesses—are their reviews terrible? Do they have limited hours? Do they lack modern features? Explain precisely how you'll exploit these gaps.
- Operational Plan: Map out your day-to-day management strategy. Who’s on staff? What software will you use? What are your security protocols?
- Marketing Strategy: Detail how you’ll attract those crucial first customers and hit your target lease-up rate.
Following this structure transforms your idea from a loose concept into a tangible, fundable project. If you're looking for a more in-depth guide, our overview on how to build a self storage business provides a detailed roadmap for this entire process.
Creating Believable Financial Projections
Get ready for some serious scrutiny here. This part of your plan has to be built on realistic assumptions grounded in solid market research. You need to map out your finances from day one right through to stable operation, which typically means forecasting for a five-year period.
These are the key financial statements you absolutely must include:
- Start-Up Cost Analysis: Itemise every single expense you can think of. Land acquisition, planning fees, construction, security systems, and your initial marketing budget all need to be on there.
- Profit and Loss (P&L) Forecast: Project your monthly revenue based on a conservative lease-up rate, factoring in rental income and any other sales. Then, subtract your operational costs to show a clear path to profitability.
- Cash Flow Projections: This shows the actual money moving in and out of the business. It’s vital for proving you can cover your expenses and loan repayments, especially in those lean early months.
Lenders are immediately suspicious of overly optimistic projections. A common mistake we see is people assuming a 90% occupancy rate within the first year. A far more realistic and defensible model shows a gradual lease-up over 18 to 36 months. It shows you understand the realities of the market.
Exploring Your Financing Options
With a robust business plan in hand, you can confidently start talking to potential lenders. The UK market has several avenues for funding a self-storage project, and each one is suited to different circumstances.
High-street banks are a common starting point. They often offer commercial mortgages that can cover a big chunk of the land and construction costs. The potential downside? They might not be familiar with the unique operational model of self-storage.
This is where specialist lenders really shine. These firms get the self-storage industry—they understand its strong cash flow and high asset value. They're often more flexible and can appreciate the nuances of a phased construction plan or a container-based model.
Other routes like joint ventures with experienced developers or seeking investment from angel investors are also worth exploring. These can be particularly good options if you're bringing a prime location to the table but lack the full capital required. No matter which path you choose, your business plan is your ticket to starting those conversations.
Launching Your Operations and Marketing Playbook
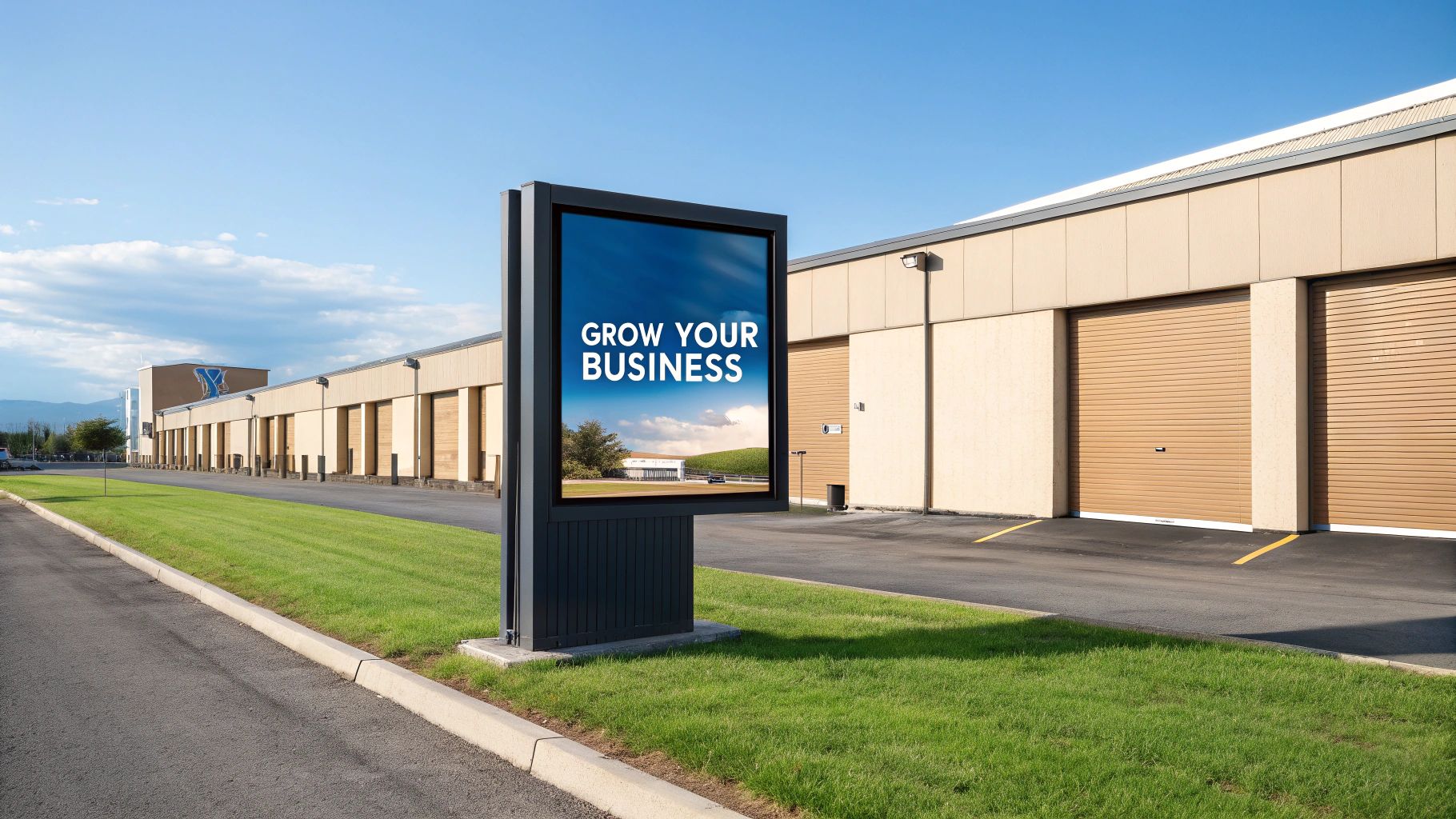
With your facility built and ready to go, the game changes. Your focus pivots entirely to operations and marketing. Getting the doors open is the starting line, not the finish. Your long-term success in the self storage as a business world hinges on two things: running a tight ship and executing a relentless marketing plan to keep those units full.
The days of tracking everything on a spreadsheet are long gone. Modern self-storage facilities run on powerful software that handles nearly every part of the business. This is the engine room of your entire operation, so picking the right system is one of the most important decisions you'll make.
Streamlining Operations with Technology
Your facility management software (FMS) will quickly become your most valuable tool. It's designed to automate all the repetitive, time-sucking tasks that can easily bog down a small team. Think of it as your digital facility manager, handling everything from collecting rent and sending invoices to controlling who gets through the gate.
A good FMS can completely transform your customer experience. You'll want to look for platforms that give customers an online portal where they can check their accounts, pay their bills, and even sign rental agreements from their own sofa. This isn't just a nice-to-have feature anymore; it's what modern consumers expect, and it dramatically cuts down on your admin workload.
Adopting technology is a huge driver of efficiency in the UK storage sector. It’s not just about software; innovation is changing the game for customer service and facility management. For example, roughly 68% of UK self storage businesses are now using artificial intelligence tools in their operations. This tech-forward approach is what allows many facilities to run lean, with an average workforce of just 2.6 staff members per site.
Building Your Marketing Engine From Scratch
Now for the fun part: getting customers through the door. Your marketing shouldn't be a scattergun approach; it needs to be a well-oiled machine, with both digital and traditional parts working in harmony. To make sure your business attracts a steady flow of renters from day one, you have to implement proven customer acquisition strategies as a core part of your playbook.
For most customers today, the journey starts with a Google search—usually something specific and urgent like "storage units near me." If you don't show up, you might as well not exist.
Here's where you need to focus your initial efforts:
- Local SEO: This is absolutely non-negotiable. Kick things off by creating and meticulously optimising a Google Business Profile. Fill out every single section with high-quality photos, accurate opening hours, and your precise address. Gently encourage your first happy customers to leave reviews, as those positive ratings are a massive factor in local search rankings.
- A Professional Website: Your website has to be clean, mobile-friendly, and dead simple to navigate. Most importantly, it should allow customers to see available unit sizes, view pricing, and—ideally—reserve or rent a unit right then and there.
- Paid Advertising (Google Ads): While your organic search presence is building up, Google Ads can deliver immediate results. Target keywords with local intent, like "self storage in [Your Town]", to capture people who are actively looking to rent right now.
To give you a clearer picture, here's a breakdown of the essential channels you'll be using to find those first critical tenants.
Essential Marketing Channels for a New Storage Facility
Marketing Channel | Primary Goal | Target Audience |
---|---|---|
Google Business Profile | Build local visibility and trust | People searching "storage near me" |
Professional Website | Convert visitors into renters | Anyone researching storage options |
Google Ads | Generate immediate, high-intent leads | Active searchers ready to rent now |
Local Partnerships | Create a steady referral stream | People in life transition (moving, renovating) |
On-Site Signage | Capture local drive-by traffic | Residents and businesses in the immediate area |
Each of these channels plays a specific role. Your digital presence casts a wide net, while your local efforts build deep community roots. Together, they create a powerful system for attracting customers.
You can’t just rely on the internet. Old-school, local marketing is still incredibly effective for self-storage. It’s all about building relationships within the community you serve.
Forging Powerful Local Partnerships
Think about who interacts with people right at the moment they realise they need storage. These are your ideal partners, and building genuine relationships with them can create a powerful referral network that costs you nothing but a bit of time.
Start by introducing yourself to these key local players:
- Estate Agents: They work with people moving house every single day. Drop off some high-quality brochures and maybe even offer a small referral fee or a special discount for their clients.
- Removal Companies: These guys are your natural allies. A good relationship here can lead to a steady stream of customers who need temporary storage during a move.
- Local Tradespeople: Plumbers, electricians, and builders often need a secure base to store tools and materials. They can become excellent, long-term tenants.
When you combine a strong digital foundation with these on-the-ground relationships, you create a complete system for attracting and keeping customers. This two-pronged approach ensures you're visible wherever your potential renters are looking—whether that's on their phone or in their local neighbourhood. It’s this complete playbook that turns an empty facility into a thriving, profitable business.
Frequently Asked Questions About the Self Storage Business
Thinking about diving into the self storage business? It’s a smart move, but like any venture, it comes with its fair share of questions. Here, we tackle some of the most common queries we hear from aspiring facility owners, using our real-world experience to give you the straight answers.
How Much Does It Realistically Cost to Start?
This is the big one, and the honest answer is: it varies dramatically. The final bill really comes down to land prices and the type of facility you want to build.
A modest container-based site on cheaper land might get off the ground in the low six figures. On the flip side, a purpose-built, multi-storey facility in a prime urban or suburban spot will almost certainly run into the millions.
Your single biggest expense, nearly every time, is the land itself. Don't forget to also budget for:
- Planning and legal fees
- Construction and materials
- Security technology (CCTV, access control)
- Management software
- A solid marketing budget to get the word out at launch
What Is a Realistic Timeframe to Reach Profitability?
Profitability all comes down to your 'lease-up' rate—how quickly you can fill those units. A well-placed, smartly marketed facility should aim for a stable occupancy of 85-90% within 18 to 36 months.
You'll likely hit your break-even point much sooner, often within the first couple of years. That’s the point where your monthly revenue consistently covers your operational costs and any loan repayments. A clever way to speed this up is with phased construction. Build an initial block of units, and only add more as demand starts to fill them. It’s a fantastic way to manage your cash flow.
A common pitfall for newcomers is underestimating the ongoing challenges of facility management. It's not just about filling units; it's about keeping them full and running the site efficiently day-to-day. You can explore some essential self storage facility management techniques for 2025 to get ahead of the curve.
What Are the Biggest Ongoing Challenges?
Once you're up and running, your primary challenges will be keeping occupancy high against local competition, handling routine property maintenance, and maintaining top-notch security.
Another constant hurdle is dealing with late payments and, occasionally, abandoned units. This isn't just a hassle; it requires you to follow strict legal procedures, so having a clear process from day one is vital. To stay competitive, you also need to adapt to what customers want, like offering climate-controlled options or more flexible access hours—all while keeping your costs lean through smart staffing and technology.
Is the UK Self Storage Market Becoming Oversaturated?
It’s more complex than a simple yes or no. While you’ll find fierce competition in major city centres, there are still countless secondary towns and growing suburban areas that are significantly underserved.
Your success hinges on doing a detailed, hyper-local market analysis. Don’t just look at the nearest city; look at the next town over. The continued rise of container storage also opens up opportunities in areas where traditional construction just isn’t financially viable. There's still plenty of room for new players, especially if you can offer a better customer experience or cater to a specific niche, like dedicated storage for students or local businesses.
Ready to turn your plans into a profitable reality? The expert team at Partitioning Services Limited has over two decades of experience in designing, manufacturing, and installing high-quality self-storage solutions across the UK. Learn how we can help you build your facility from the ground up by visiting us at https://psllimited.co.uk.
Maximise Space with Commercial Mezzanine Floors
When you’re staring up at the high ceilings in your facility, all that empty air can feel like a huge missed opportunity—a constant, nagging reminder of untapped potential. This is where commercial mezzanine floors come in. They are the go-to strategic solution for transforming that vertical void into valuable, productive floor space.
It’s best not to think of it as complex, disruptive construction. Instead, see it as unlocking a new, highly functional chapter for your building, but without the headache and expense of a full-blown relocation.
Unlock Your Hidden Vertical Space
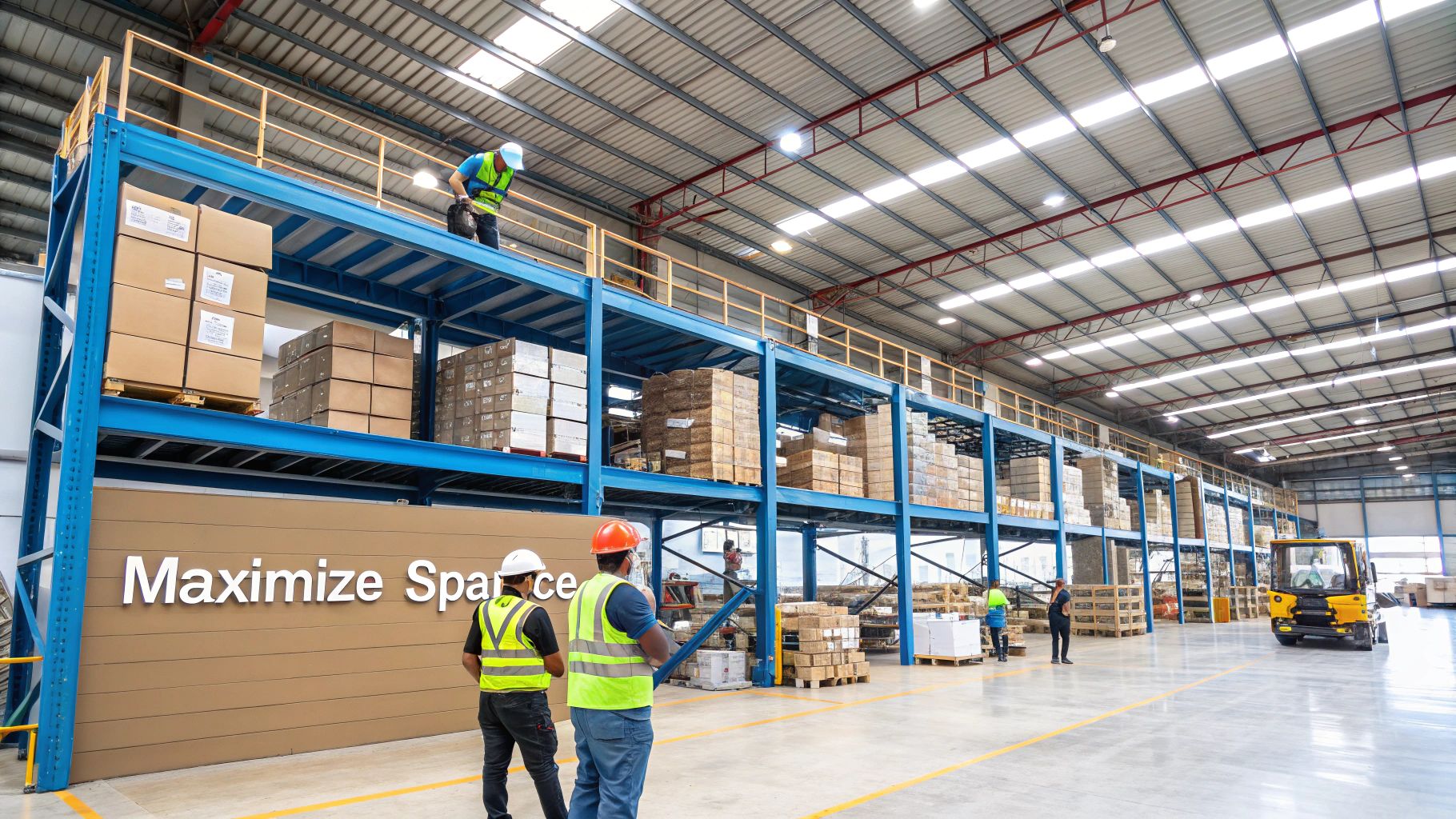
For any UK business looking to expand its operational footprint, a commercial mezzanine floor is an incredibly powerful tool. It’s essentially an intermediate, semi-permanent level installed between the main floors of a building, creating brand-new space seemingly out of thin air. This isn't about adding a full, traditional second storey; it's a far more elegant and efficient approach.
Just imagine your warehouse, retail unit, or office. Now, picture a sturdy, custom-engineered platform sitting smartly above the existing floor. Suddenly, you have a brand-new area ready for whatever your business needs most, whether that's more storage, office space, or a production line. This clever use of vertical space is a genuine game-changer for businesses feeling the squeeze.
More Than Just an Extra Level
If you only see a mezzanine as an 'extra level,' you’re missing its true value. It’s a strategic asset that delivers tangible benefits with remarkable speed and efficiency. The proof is in the numbers, with the global mezzanine floor industry projected to hit USD 24.57 billion by 2030. This boom is fuelled by businesses just like yours demanding cost-effective, scalable solutions.
A mezzanine floor essentially doubles your usable floor area without expanding your building’s footprint. It’s a cost-effective expansion that enhances workflow and optimises your current lease.
Core Benefits for Your Business
The advantages of installing commercial mezzanine floors go far beyond simply getting more room. They represent a smart, strategic investment in your operational capacity. The core benefits really boil down to this:
- Cost-Efficiency: It is significantly more affordable than relocating to larger premises or undertaking a major building extension. Think of the savings on rent, rates, and hefty construction costs.
- Rapid Installation: Because the components are prefabricated off-site, the installation process is incredibly fast—often taking just a few weeks. This means minimal disruption to your daily operations.
- Ultimate Flexibility: These structures are typically demountable. If your business needs to move, the mezzanine can be dismantled and reinstalled at your new location, protecting your investment.
What’s more, these platforms are fully customisable. They can be designed to house additional offices, perhaps using partitions to create defined, quiet work areas. You can learn more about how to achieve this by checking out our guide on maximising space with partitioning systems.
By turning unused overhead space into a functional asset, a mezzanine tackles your immediate needs while future-proofing your facility for whatever comes next.
Understanding Your Mezzanine Design Options
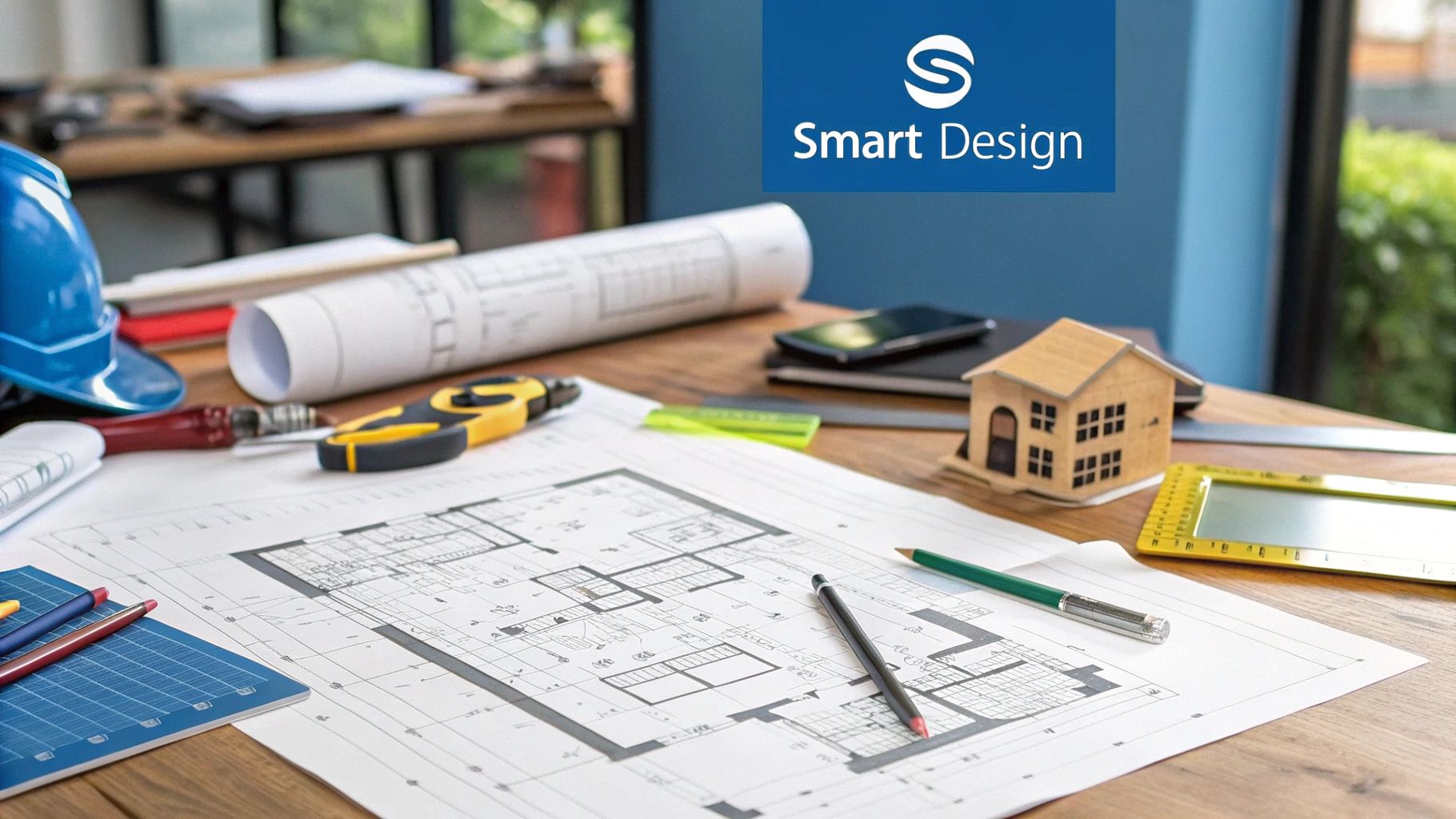
A commercial mezzanine floor is so much more than just a platform of steel and wood; it's a bespoke solution, engineered to slot perfectly into your business's operational DNA. To get that perfect fit, you first need to get to grips with the fundamental design choices that will form its blueprint. These decisions are critical, as they directly shape its function, cost, and long-term value.
Thinking about the structure itself is always the best place to start. A mezzanine isn’t just dropped into your building; it's integrated in a very specific way. The two main approaches offer their own distinct advantages, depending entirely on your existing setup and what you hope to achieve.
Freestanding vs Integrated Structures
The most common approach you’ll see is the freestanding mezzanine. Think of it like a massive, incredibly strong table. It stands on its own legs, completely independent of your building’s walls or main framework. All the weight it carries is transferred directly down to the floor slab through its own set of steel columns.
This independence is its greatest asset. It gives you ultimate flexibility, allowing installation in almost any building with enough headroom. Better yet, if you ever decide to relocate, it can be dismantled and taken with you.
The alternative is an integrated or rack-supported mezzanine. With this setup, the mezzanine floor is built directly into a new or existing pallet racking system. The racking uprights cleverly pull double duty, supporting both the pallets of goods below and the new floor level above. It's an incredibly space-efficient solution for warehouses and distribution centres that need to combine high-density storage with extra floor space for tasks like picking, packing, or light assembly.
The choice between freestanding and rack-supported isn't just a technical one—it's strategic. Freestanding gives you the versatility for varied uses like offices or production areas, while rack-supported is the definitive space-saver for intensive storage operations.
Nailing this choice sets the stage for a truly optimised space. For businesses in the self-storage sector, there are even more specialised designs to think about. You can explore some of these by reading about innovative mezzanine floor designs to optimise your self-storage space in our detailed guide.
Defining Load Capacity and Decking
Once you’ve settled on the structural type, the next critical factor is load-bearing capacity. This simply means how much weight your new floor can safely hold, and it's measured in kilonewtons per square metre (kN/m²). This isn't a one-size-fits-all number; it has to be precisely matched to whatever you plan to use the floor for.
Here are a few typical load ratings to give you an idea:
- Light Office Use (approx. 3.5 kN/m²): Perfect for standard office furniture, computer gear, and everyday foot traffic.
- Standard Storage (approx. 4.8 kN/m²): This is the most common rating. It's designed for hand-loaded storage, light goods, and general picking areas.
- Heavy-Duty Storage (approx. 7.5 kN/m²): Engineered for areas where you'll be using pallet trucks or storing heavier, bulkier items.
- Heavy Machinery/Production (10+ kN/m²): This is a specialist capacity, built to support production equipment, heavy plant, or high-density racking systems.
Getting this wrong is simply not an option, as it’s a matter of safety and legal compliance. Any professional supplier will carry out a thorough assessment to make sure the structure is specified correctly for your needs.
Finally, the decking material is the surface you'll actually be walking and working on. The industry standard, and the most cost-effective choice, is 38mm particle board. It’s ideal for the vast majority of storage and office applications. For more demanding environments, you might consider other options:
- Steel Grating: This allows light and air to pass through, which is often a requirement of fire regulations in certain layouts.
- Composite Decking: A highly durable and moisture-resistant option that provides a more premium, hard-wearing finish.
Essential Safety and Access Features
A useful mezzanine is a safe mezzanine. Period. The design absolutely must include features that ensure your team can use the space securely and efficiently. Key elements here are custom-designed staircases for people to get up and down, and pallet gates for safely loading and unloading goods with a forklift.
Those gates are a non-negotiable safety feature. A simple swing gate or an up-and-over pallet gate creates a protected edge, preventing dangerous falls when moving stock between levels. When you combine this with robust handrailing and kick plates around all exposed edges, you ensure your new space is fully compliant and, most importantly, safe for your team.
Navigating UK Building Regulations and Compliance
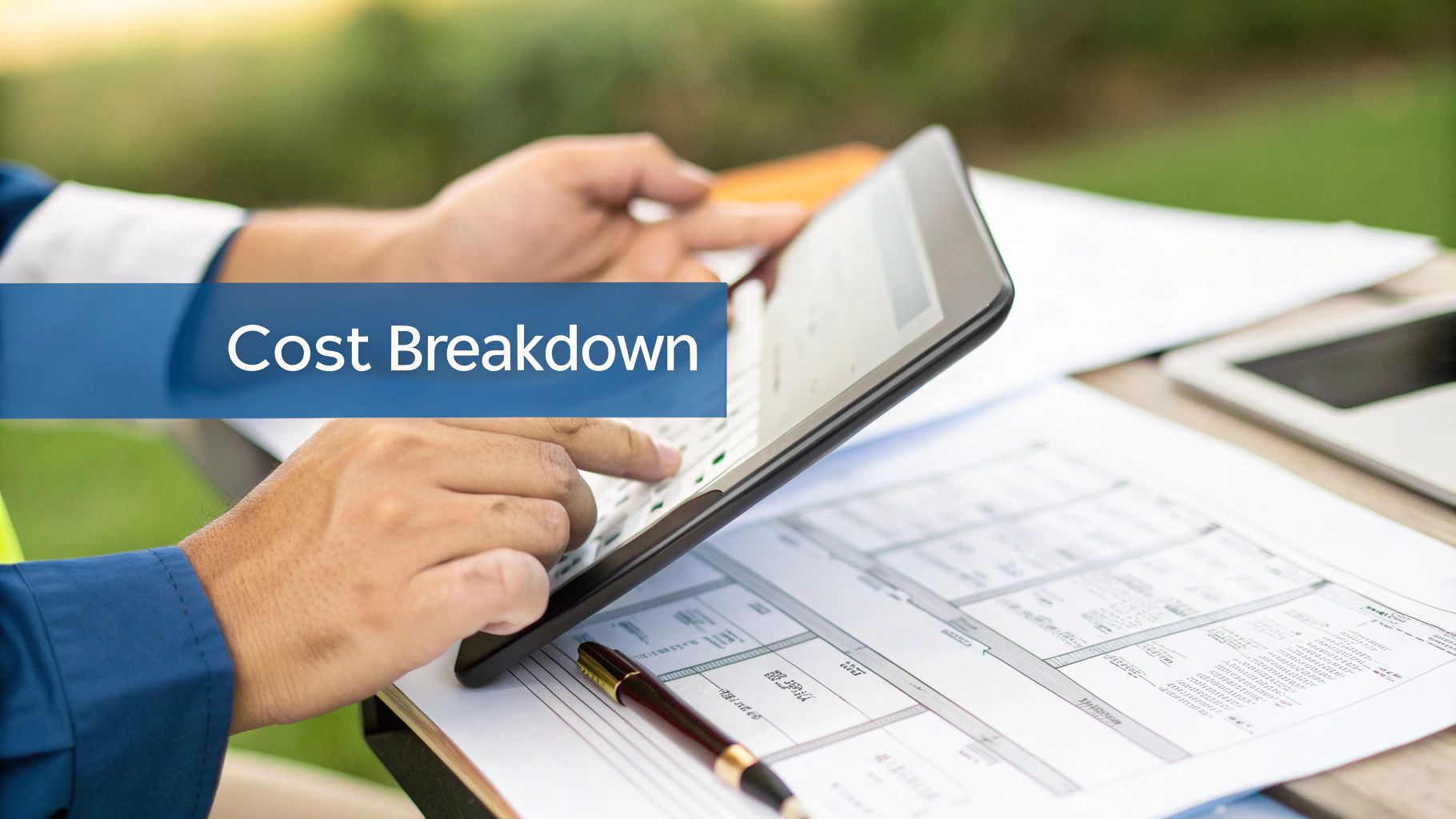
Getting a commercial mezzanine floor installed successfully isn't just about clever design and solid construction. It's about making sure every single nut, bolt, and beam is fully compliant with UK law. While this part of the process can feel a bit intimidating, it’s a non-negotiable step that guarantees the safety and legality of your new space.
It helps to think of compliance not as a roadblock, but as a built-in quality control checklist for your investment. The two main hurdles you'll face are Building Regulations approval and, in some situations, planning permission. Getting your head around the difference between them is the first step to a smooth, stress-free project.
Planning Permission vs. Building Regulations
It’s a common mix-up, but these two serve entirely different functions. Planning permission is all about the bigger picture—how a development impacts the local community and environment. It looks at things like the building's external appearance and how it will be used.
Building Regulations, on the other hand, focus squarely on the health and safety of the people who will be using the building. They set out the technical standards for design and construction, covering everything from structural integrity and fire safety to accessibility. For virtually all commercial mezzanine floors, you absolutely must get Building Regulations approval.
The good news? Most mezzanine projects don't need full planning permission. Because they’re usually classed as demountable, internal structures, they often fall under ‘permitted development rights’. There is a critical exception, though: if the mezzanine is going to increase permanent retail floor space or change the building's exterior, you will almost certainly need planning permission.
The Non-Negotiables of Building Control
When you submit your project, a building control officer will review your plans against a strict set of criteria. Their one and only goal is to sign off on a structure that's fundamentally safe and fit for purpose. This means they’ll be putting several key areas of your mezzanine design under the microscope.
Three of the most critical aspects they will examine are:
- Structural Safety: The design has to prove the mezzanine can safely take the weight it's intended for. This involves complex calculations for the steelwork, columns, and foundations to ensure they can support people, equipment, or stock without any risk of failure.
- Fire Safety: This is absolutely paramount. Your structure might need to be fire-rated, typically for 60 minutes, to protect it from collapsing in a fire. This often means cladding columns in special protective materials and installing a fire-rated suspended ceiling underneath.
- Safe Access and Escape: The plans must show clear and safe ways for people to escape in an emergency. This includes the number, location, and design of staircases, making sure they’re adequate for the number of people who will be using the new level.
Navigating the fine print of compliance is a complex but vital job. A reputable supplier will manage the entire Building Regulations application for you, dealing with approved inspectors to ensure a seamless approval and a fully certified installation.
Staying Current with Regulatory Changes
Building codes aren't set in stone; they're regularly updated to reflect new safety standards and construction techniques. It is vital to stay informed about the latest updates, such as the Section 6 of Scottish Building Regulations, to ensure your mezzanine project meets all current compliance requirements.
This constant evolution means that a design that was perfectly compliant a few years ago might not pass muster today. Partnering with an expert who stays on top of these changes is your best insurance against costly rework or a failed inspection. For a deeper dive into the specifics, you can find a wealth of information by exploring our detailed guide to UK building regulations. Ultimately, ensuring your project meets every standard is the only way to protect your staff, your business, and your investment.
Calculating the Cost and Your Return on Investment
Let's talk numbers. When you're considering a significant upgrade like a commercial mezzanine floor, getting a firm grip on the finances is essential. It’s easy to look for a simple price per square metre, but the reality is that the total investment is shaped by a unique blend of factors specific to your project. Looking past a generic estimate is the key to seeing the true value and building a solid business case.
The final cost isn't just about size; it's about what you plan to do with the space. A light-duty office mezzanine has completely different structural demands from one designed to support heavy machinery or high-density pallet racking. Every one of these requirements influences the design, the materials, and ultimately, the price tag.
Key Variables That Shape Your Investment
Several core elements will directly influence your total project cost. Thinking through these factors with your supplier is what leads to a far more accurate and reliable quotation. Think of them as the building blocks of your investment.
The most significant variables include:
- Load Capacity: As we've touched on, what you'll use it for dictates the strength needed. A floor for light storage will naturally be more affordable than one engineered for heavy industrial applications that demand a higher kN/m² rating.
- Custom Features: Your specific operational needs will determine the extras. This covers the number and type of staircases, whether you need pallet gates for safe goods handling, and any specialised handrailing.
- Site Access and Complexity: The condition of your building really matters. An open, clear warehouse is much simpler to work in than a facility riddled with obstructions, tight access points, or an uneven floor slab that needs levelling work first.
- Fire Protection: Depending on its use and size, Building Regulations may require your mezzanine to be fire-rated, typically for 60 minutes. This involves adding fire-resistant cladding to columns and installing a suspended ceiling, which adds to the cost but is a critical, non-negotiable safety measure.
This is exactly why a generic online calculator can be so misleading. Here in the UK, commercial mezzanine floors have become a go-to solution for tackling space constraints, with construction typically priced between £75 and £150 per square metre. Where your project falls in that range depends entirely on the factors above.
Beyond the Upfront Cost: The Real ROI
The true financial power of a mezzanine isn't just in its installation cost but in its return on investment (ROI). This is where the numbers really start to work in your favour. The ROI comes from a combination of direct cost avoidance and massive operational gains.
The most compelling financial argument for a mezzanine floor is a direct comparison. Pit the one-time cost of the mezzanine against the endless, escalating expense of leasing additional commercial space. Over a few short years, the mezzanine pays for itself.
Imagine your business needs an extra 500 square metres of space. You have three paths: lease another unit, build an extension, or install a mezzanine. Leasing means you’re stuck with ongoing rent, business rates, and service charges that bleed cash year after year. A building extension is a huge, capital-intensive project, often bogged down by long timelines and major disruption.
A mezzanine, on the other hand, is a one-off capital expense. Once it's paid for, it generates value indefinitely. Just look at how quickly these projects come together.
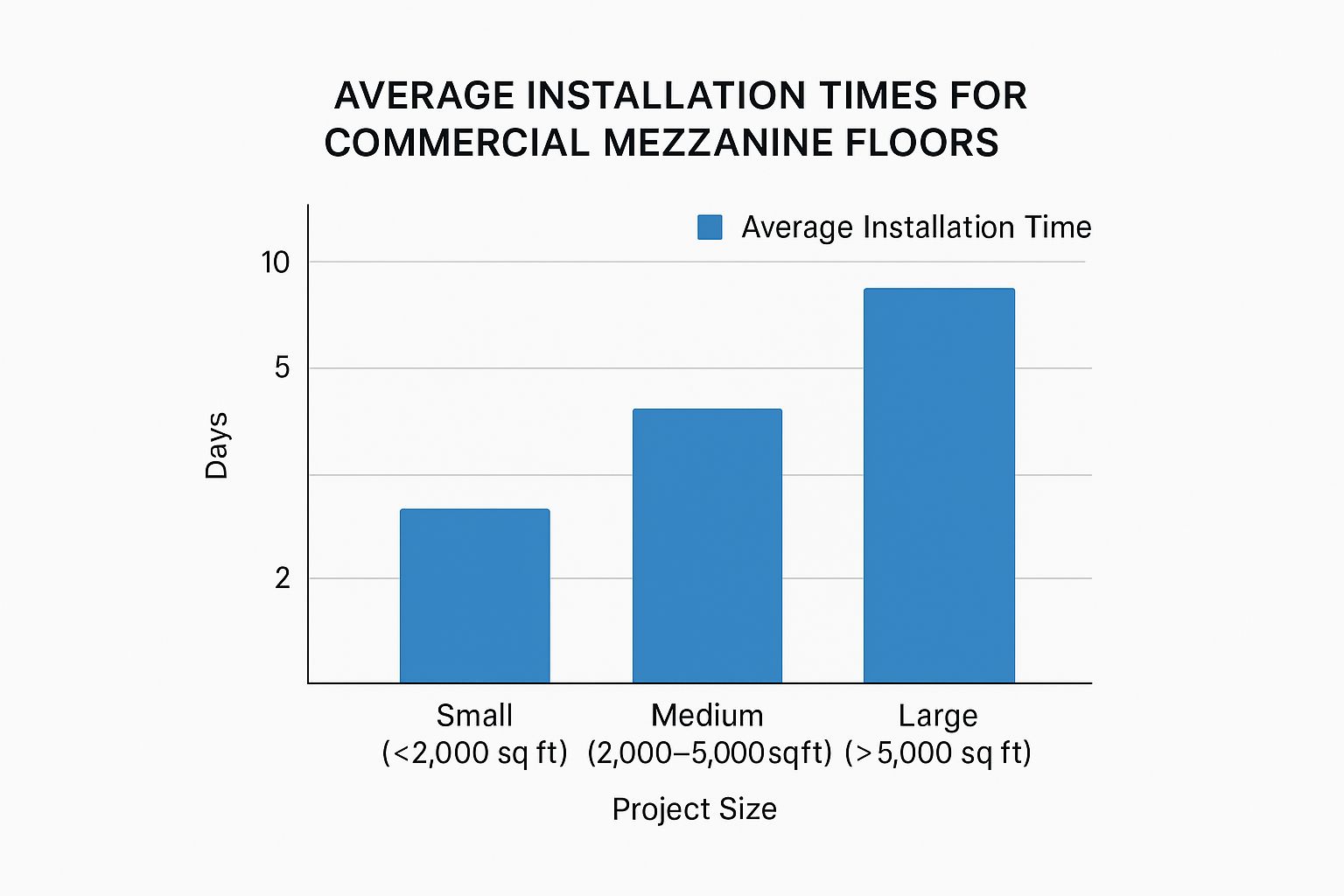
As you can see, even large-scale mezzanine projects can be completed in a matter of weeks, not months. This minimises operational downtime and gets you to that return on investment much faster.
To give you a clearer picture, this table breaks down the potential costs of each option over a 5-year period.
Cost Comparison: Mezzanine Floor vs Traditional Expansion
This table illustrates the potential cost savings of installing a commercial mezzanine floor compared to leasing new space or constructing a building extension over a 5-year period.
Expense Type | Commercial Mezzanine Floor (500 sq m) | Leasing New Warehouse Space (500 sq m) | Building Extension (500 sq m) |
---|---|---|---|
Initial Outlay | £50,000 (Avg. £100/sq m) | £12,000 (Deposit + Legal) | £600,000 (Avg. £1,200/sq m) |
Annual Rent | £0 | £40,000 (Avg. £80/sq m) | £0 |
Annual Business Rates | £0 (Often exempt) | £20,000 (Avg. 50% of rent) | £30,000 (Increased property value) |
Annual Service Charge | £0 | £5,000 | £0 |
Maintenance/Repairs | £500 (Minimal) | £2,500 (Variable) | £3,000 (New structure) |
Total 5-Year Cost | £52,500 | £349,500 | £765,000 |
The numbers speak for themselves. While a mezzanine requires an initial investment, its long-term cost is drastically lower than the alternatives, freeing up capital that can be reinvested into growing your business.
How a Mezzanine Drives Tangible Value
Calculating the full ROI means looking at every financial benefit the new space provides. It’s a multi-faceted value proposition that directly strengthens your bottom line.
Here’s how a mezzanine actively boosts your finances:
- Increased Operational Capacity: More space means more capacity for stock, production, or people. This allows your business to take on more work and generate more revenue, all from the same premises.
- Improved Workflow Efficiency: By creating dedicated zones for different business functions—like storage, packing, and administration—you can streamline processes, cut down on wasted movement, and make your team more productive.
- Potential Business Rates Avoidance: In many cases, because a mezzanine is classified as a demountable structure, it does not increase the rateable value of your property. This can lead to substantial, ongoing tax savings compared to a permanent extension.
When you're budgeting, it's also helpful to have a broad sense of market prices. For more general budgeting, especially for the raw materials involved, a tool that predicts construction material costs can be invaluable. By combining these direct and indirect financial benefits, you can build a robust business case that demonstrates clear, measurable, and long-term value.
How UK Industries Use Mezzanine Floors
Theory is one thing, but seeing how mezzanines work in the real world is where the penny really drops. Across the UK, smart businesses are using these clever structures to solve nagging space problems, completely transforming their facilities from the inside out. It’s one thing to look at a technical drawing, but it’s another to see how other companies have already put them to work and reaped the rewards.
From huge warehouses to busy high-street shops, these examples show that a mezzanine is far more than just an extra floor. It's a strategic move that drives growth, boosts efficiency, and even improves the customer experience. Each story starts with a familiar business headache and finishes with a clear, positive outcome.
Case Study 1: The Warehouse That Doubled Its Stock
A third-party logistics (3PL) provider in the Midlands had a problem every growing business dreams of—and dreads. Their warehouse was at bursting point. With demand through the roof, they were actually turning away new contracts simply because they had nowhere to put the stock. Moving was out of the question financially, and all that empty air above their heads in the high-ceilinged unit felt like a massive wasted opportunity.
The answer was a freestanding, multi-tier mezzanine that created over 1,000 square metres of new space right inside their existing warehouse. The ground floor was kept clear for bulky pallet storage and processing incoming goods. Meanwhile, two brand-new levels above were kitted out with high-density shelving, perfect for smaller, fast-moving items.
The results were instant and impressive:
- Doubled Inventory Capacity: The business could suddenly hold twice the amount of stock, letting them take on new clients with confidence.
- Streamlined Picking Process: By separating bulk pallets from single-item picking, they slashed their pick times by an estimated 30%, getting orders out the door much faster.
- Avoided Relocation Costs: The entire project cost a fraction of what they would have spent on the expense and massive disruption of moving to a new, larger facility.
Case Study 2: The Retailer That Enhanced Customer Experience
A popular independent fashion retailer in Manchester was ready to expand its collection but was hemmed in by its single-floor layout. It’s in situations like this where the versatility of mezzanines really shines, especially in the demanding Commercial Retail industry. For this shop, the mission was to create a premium showroom for a new designer range without eating into their precious ground-floor retail space.
A sleek, lightweight mezzanine was installed at the back of the store. Designed with glass balustrades and a stylish open staircase, it immediately created an exclusive, boutique-like atmosphere. This new level became a dedicated space for personal styling sessions and showcasing high-end pieces, completely elevating the customer's shopping journey.
In the UK retail sector, where average customer conversion rates hover between 20% and 40%, creating a memorable in-store experience is everything. Mezzanines give retailers a fantastic tool to build engaging, multi-level environments that directly contribute to lifting this crucial performance metric. You can explore more about how mezzanines increase retail conversion rates to see the real financial impact.
The new showroom didn't just look good; it directly boosted sales and customer loyalty. It was proof that a well-designed mezzanine can be one of the most powerful sales tools you have.
Case Study 3: The Office That Fostered Innovation
An expanding London tech company was grappling with a classic open-plan office problem: it was noisy, distracting, and wasn't working for either focused tasks or team collaboration. They desperately needed different kinds of workspaces—quiet pods, breakout areas, and proper meeting rooms—but couldn't face the eye-watering cost and upheaval of moving to a new office in the city.
Their solution was to build a commercial mezzanine floor over part of their existing office. They designed this new upper level specifically for collaboration, filling it with comfortable seating, whiteboards, and informal meeting spots. The space created underneath the mezzanine was then converted into quiet, partitioned offices perfect for deep, focused work.
This smart division of space completely changed the company's culture and productivity. It gave employees the freedom to pick an environment that matched their task, nurturing both focused concentration and spontaneous teamwork. Not only did the project save them from an incredibly expensive relocation, but it also created a more dynamic and effective workplace that directly fuelled their innovative spirit.
Common Questions About Commercial Mezzanines
Even after seeing all the benefits, design options, and rules, you probably have a few practical questions buzzing around. That’s perfectly normal. Putting a commercial mezzanine floor in your facility is a big decision, and you need to be confident before moving forward.
To help clear things up, we’ve put together a few of the most common questions that business owners and facility managers ask us. Here are some straightforward answers to the things that often come up.
Do I Need Planning Permission for a Commercial Mezzanine Floor?
This is easily one of the most frequent questions we get, and the answer is usually good news. In the UK, you often don’t need planning permission for a mezzanine. Most are classed as demountable, internal structures, which means they typically fall under permitted development rights.
However, there are some important exceptions. You will almost certainly need planning permission if the new floor is going to be used for permanent retail sales space or if the project changes the outside of your building in any way.
The most important thing to remember is this: while planning permission might not be needed, Building Regulations approval is always mandatory. Every single mezzanine installation has to be reviewed and signed off to make sure it meets strict standards for structural integrity, fire safety, and access.
A good supplier will handle this entire process for you, working with the inspectors to make sure everything is fully compliant.
How Long Does a Mezzanine Floor Installation Take?
Business owners are often pleasantly surprised by how quickly a mezzanine project can come together. The on-site build is remarkably fast because most of the work—like fabricating the steel and other parts—is done off-site in a controlled factory setting.
Once the design is finalised and all the components are manufactured (which usually takes about four to six weeks), the actual on-site installation is often finished in just one to two weeks. Of course, the exact timeline will depend on how big and complex your project is.
To keep disruption to your business at a minimum, a professional installation team will work with you to create a schedule that fits your operations. This might mean scheduling the build over weekends, in the evenings, or in stages to keep your company running smoothly.
What Load Capacity Can a Mezzanine Floor Support?
There’s no such thing as a "standard" load capacity, because every mezzanine is custom-engineered for its specific job. This isn't a one-size-fits-all product. The structure's strength is calculated precisely based on how you plan to use the new space.
To give you an idea of what that means, here are a few typical load ratings:
- Light-Duty Office (3.5 kN/m²): Perfect for a standard office setup with desks, computers, and normal foot traffic.
- Medium-Duty Storage (4.8 kN/m²): This is a very common specification, ideal for hand-loaded shelving, packing areas, and general light goods storage.
- Heavy Industrial Use (10+ kN/m²): For the really demanding jobs, like supporting heavy machinery, production lines, or pallet racking, the structure can be engineered to handle much higher loads.
Your supplier will carry out a detailed assessment of what you need to design a structure that is perfectly and safely fit for purpose.
Can I Move or Extend a Mezzanine Floor Later?
Yes, and this flexibility is one of the biggest perks of a mezzanine. Most commercial mezzanine floors are designed as modular systems where the steel parts are bolted together, not welded to your building.
This clever design means the floor can be:
- Dismantled and Relocated: If your business moves, the mezzanine can be taken down, transported, and reassembled at your new site.
- Extended or Reconfigured: As your needs change, the mezzanine can be modified. You can easily add to its footprint or change the layout to suit new workflows.
This scalability makes a mezzanine a truly sustainable, long-term asset. It isn’t just a fix for today; it’s an investment that can grow and adapt with your business, protecting its value for years to come. For a closer look at the different types available, you can explore the options for commercial mezzanine floors and see how they can be tailored to specific industrial needs.
Ready to unlock the hidden potential in your facility? The team at Partitioning Services Limited has over 24 years of experience in designing, manufacturing, and installing high-quality, compliant commercial mezzanine floors across the UK and Europe. We manage the entire process, from initial concept to final sign-off, ensuring your project is delivered on time and on budget. Transform your space by visiting us at https://psllimited.co.uk to schedule your free consultation and site survey today.
Level Up Access and Safety with Rolling Staircase Units
Rolling staircase units solve two major challenges in self-storage facilities: safe access to upper-level units and improved efficiency. With self-storage facilities increasingly using multi-level designs to maximise space, traditional ladders and fixed staircases often fall short in meeting modern safety and usability standards. Rolling staircase units address these issues with features like mobility, stability, and compliance with OSHA safety regulations.
Key Takeaways:
- Accessibility: Rolling staircases make it easier for tenants and staff to reach upper-level units, especially when handling heavy or oversized items.
- Safety: Slip-resistant steps, handrails, and secure locking systems reduce the risk of falls and accidents.
- Efficiency: Their mobility allows a single unit to serve multiple areas, saving space and reducing operational delays.
- Compliance: Designed to meet federal safety standards, minimising liability and ensuring a safer environment.
By integrating rolling staircase units, facilities can improve tenant satisfaction, reduce safety risks, and optimise operations. These units are a practical solution for modernising self-storage spaces and keeping up with industry demands.
Access and Safety Problems in Self-Storage Facilities
As self-storage facilities grow taller to make the most of their space, they face new challenges that affect both accessibility and safety. These issues not only complicate daily operations but also have a direct impact on tenant satisfaction and overall profitability. Facility operators need to address these concerns to stay competitive and compliant with safety standards.
Difficulty Reaching Upper-Level Units
Getting to units on upper levels is a common frustration for tenants. Traditional ladders and fixed staircases often fall short when it comes to meeting the diverse needs of customers - especially when heavy or oversized items need to be moved. This problem is even worse during busy times when tenants compete for limited equipment.
Climbing ladders while carrying storage items is physically demanding and can lead to longer visits and mounting frustration. For elderly tenants, those with mobility challenges, or business customers managing bulky inventory, the struggle is even greater. Many of these customers require staff assistance, which not only slows operations but also creates bottlenecks. These physical challenges also introduce safety risks, which we’ll cover next.
Safety Risks for Tenants and Staff
The lack of proper access solutions in self-storage facilities can lead to serious safety concerns. Traditional ladders and other basic methods often increase the risk of falls and injuries, particularly when tenants are carrying heavy items. Without robust safety protocols, these hazards can quickly escalate.
"In a self-storage environment, the significance of security measures - ranging from 24-hour surveillance to daily property inspections - cannot be overstated. They serve as the frontline of defense." - Josh Leykam, Vice President of Underwriting at MiniCo
Poor lighting further amplifies these risks. Research consistently shows that better lighting can significantly reduce both accidents and crime. Facilities that operate around the clock face additional challenges, as extended access hours often come with minimal staff on-site, increasing the likelihood of accidents.
These safety concerns don’t just affect tenants - they also disrupt operations. Staff members who must assist with access or respond to incidents are pulled away from other duties, reducing overall efficiency.
Reduced Operational Efficiency
Inefficient access systems can have a ripple effect that hurts both profitability and the customer experience. When tenants encounter delays or difficulties, their visits take longer, reducing the facility’s overall capacity to handle peak demand. This inefficiency is particularly costly during busy periods when quick turnover is critical.
Customer dissatisfaction from repeated access issues often drives tenants to look for alternative storage options. This not only increases turnover but also raises marketing expenses to attract new customers. Additionally, the extra staff support required to address these challenges adds to operational costs.
A recent survey of Sensorberg's international clients highlighted the financial upside of addressing these issues: facilities that adopted smart access technology saw a 30% return on investment within the first year.
"One thing that remains constant is operators' desire to ensure happy, loyal customers. Site safety and security play a large role in that outcome, which means your facility must have proper lighting. Poorly lit exteriors and dark hallways not only make a poor impression, but they also open your business to crime and accidents, leave staff and tenants feeling vulnerable, and drive prospects running to your competitors." - Inside Self-Storage magazine
Tackling these challenges is essential for improving safety, efficiency, and customer satisfaction. To learn more about solutions tailored to these problems, check out our self-storage solutions or explore how Rolling Staircase Units for Self Storage Facilities can elevate your facility’s standards.
How Rolling Staircase Units Fix Access and Safety Problems
Rolling staircase units tackle the dual challenges of accessibility and safety that self-storage facilities often face. These mobile and stable solutions are designed to meet modern facility demands without compromising on safety. Unlike fixed staircases or traditional ladders, rolling staircase units offer flexibility and reliability, making them a smart choice for dynamic storage environments.
Key Features of Rolling Staircase Units
Rolling staircase units come packed with features that directly address the needs of self-storage facilities, offering practical solutions for access and safety.
One standout feature is their mobility. Thanks to wheeled casters, these units can be easily moved around the facility, even in tight spaces. Some advanced models include 360° swiveling locking casters, allowing a single person to reposition them effortlessly. This flexibility eliminates the need for multiple fixed staircases, saving both space and installation costs.
Stability is another area where these units excel. They come equipped with weight-activated caster retraction systems that secure the staircase in place during use, eliminating the wobble often associated with traditional ladders.
Safety is further enhanced with slip-resistant steps, which improve traction and reduce the risk of slips - especially critical when tenants are carrying heavy or bulky items. Handrails and guardrails provide additional support, making these units especially helpful for elderly tenants or those with limited mobility.
Designed to handle the demands of large facilities, these units are available in configurations ranging from 2 to 15 steps, allowing operators to choose the right fit for their specific needs. For more details on tailored options, check out our Rolling Staircase Units for Self Storage Facilities.
Meeting Health and Safety Standards
Rolling staircase units comply with all relevant Cal/OSHA and OSHA regulations, ensuring they meet federal safety requirements. These include strict guidelines for step dimensions, slip resistance, and load capacity.
For units with a top step height of 4 feet (1.2 m) or higher, handrails must be installed with a vertical height between 29.5 inches (75 cm) and 37 inches (94 cm). Additionally, movement prevention systems are built into the design, addressing one of the biggest safety concerns with mobile access equipment. By adhering to these standards, facilities can significantly lower the risk of accidents and create a safer environment for both tenants and staff.
Enhancing the Tenant Experience
Rolling staircase units don't just improve safety - they also make life easier for tenants. The combination of a stable platform and secure handrails gives tenants confidence when accessing upper-level storage, even when carrying heavy items. Their user-friendly design allows for safe, self-paced use, reducing physical strain and improving comfort.
Operational efficiency also gets a boost. Because these units can be quickly moved to where they're needed, tenants spend less time waiting for access equipment, even during busy periods. Plus, their professional and purpose-built appearance reflects positively on facility management, showcasing a commitment to safety and customer care.
For operators seeking to upgrade their facilities, our self-storage solutions offer a range of options to improve safety and tenant satisfaction. Investing in proper access equipment not only reduces liability but also enhances tenant retention and streamlines operations, contributing to better overall performance. Rolling staircase units are a practical addition that seamlessly integrates into modern storage facility designs.
sbb-itb-55d1b84
Rolling Staircase Units vs Other Access Solutions
When choosing access solutions for self-storage facilities, operators often weigh the pros and cons of rolling staircase units, traditional ladders, and fixed stairs. Each option impacts safety, efficiency, and cost in different ways.
Benefits of Rolling Staircase Units
Rolling staircase units offer a safer alternative to traditional ladders and fixed stairs. According to industry statistics, falls account for nearly 15% of fatal accidents in warehouse environments, and 43% of fatal ladder-related incidents were reported over a decade. This makes safety a top priority for facility operators.
"Rolling stairs are much safer than A-frame ladders. They are less likely to tip over because they are mounted on casters and have handrails that provide additional stability." - Great Boards
One standout advantage of rolling staircase units is their mobility. Unlike fixed stairs, these units can be moved easily around the facility, eliminating the need for multiple fixed installations. This not only saves on installation costs but also optimises space usage. A single rolling unit can serve multiple areas, making it a cost-effective and space-efficient choice. For more details, visit our page on Rolling Staircase Units for Self Storage Facilities.
Operational efficiency is another key benefit. Rolling staircase units can be quickly repositioned without the hassle of disassembly or complex setups. This reduces delays during busy times and allows staff to allocate resources more effectively.
Stability is a game-changer when comparing access solutions. Rolling staircase units provide a stable platform with handrails, reducing physical strain and instilling confidence in users, especially when handling heavy or bulky items. In contrast, traditional ladders demand constant balance adjustments, which can be physically taxing and unsafe.
From a compliance standpoint, rolling staircase units are designed to meet OSHA regulations for Walking-Working Surfaces. This helps facilities avoid common safety violations and minimises liability risks for operators.
Comparison Table: Rolling Staircase Units vs Other Solutions
Feature | Rolling Staircase Units | Traditional Ladders | Fixed Stairs |
---|---|---|---|
Safety Level | High – stable platform with handrails | Low – high fall risk, balance required | Medium – stable but location-limited |
Mobility | Excellent – easily repositioned | Good – portable but setup required | None – permanent installation |
Space Efficiency | Good – single unit serves multiple areas | Excellent – compact storage | Poor – dedicated space required |
User Confidence | High – stable, secure platform | Low – requires balance and skill | High – familiar stair climbing |
Load Capacity | High – designed for heavy items | Limited – restricted carrying capacity | High – hands-free climbing |
Setup Time | Minimal – roll into position | Quick – unfold and position | None – always ready |
Maintenance | Low – periodic inspections | Low – basic checks | Medium – structural inspections |
Initial Investment | Medium – higher than ladders | Low – most affordable option | High – construction and installation |
Long-term Value | Excellent – versatile and durable | Fair – replacement needs | Good – permanent solution |
OSHA Compliance | High – purpose-built for regulations | Challenging – frequent violations | Good – meets building codes |
This comparison highlights why rolling staircase units are becoming the preferred choice for many operators. While traditional ladders are more affordable upfront, they pose serious safety risks and compliance challenges. Fixed stairs, though stable, lack the flexibility needed in dynamic storage environments.
"When compared to a folding ladder, a rolling ladder provides enhanced levels of safety and stability." - Wildeck
Balancing safety, efficiency, and cost, rolling staircase units emerge as the ideal solution. They address the limitations of both ladders and fixed stairs while improving overall facility operations. For more information on how Partitioning Services Limited can enhance your self-storage facility, visit our PSL homepage.
Up next, we'll explore how to seamlessly integrate rolling staircase units into your facility's design to maximise safety and efficiency.
Adding Rolling Staircase Units to Self-Storage Facility Design
Incorporating rolling staircase units into your self-storage facility requires careful planning to ensure safety, efficiency, and a solid return on investment. Whether you're building a new facility or upgrading an existing one, a thoughtful approach can make all the difference.
Customising Staircases for Facility Needs
Rolling staircase units should be tailored to meet the specific demands of your facility. These customisations include adjusting for your building's dimensions, layout challenges, and operational requirements to achieve both safety and functionality.
For example, the height and width of the staircases must fit seamlessly within your building's clearances and traffic patterns. If your facility caters to residential customers, you might need wider platforms to handle larger items. On the other hand, business-focused storage areas may benefit from more compact designs that maximise aisle space.
"PSL offers bespoke designs tailored to the unique shape and dimensions of your building, ensuring optimal utilisation of available space." – PSL
Custom features, like removable handrails, add flexibility, especially during busy periods when adaptability is crucial for smooth operations. To get the best results, work with experienced professionals who can guide you through the design process. This typically involves detailed site surveys, AutoCAD drawings, and a thorough analysis of traffic flow to address potential challenges before installation. The result? A staircase design that enhances both space utilisation and operational efficiency.
For more details, check out Rolling Staircase Units for Self Storage Facilities.
Integrating with Other Systems
Rolling staircase units work best when seamlessly integrated with other systems in your facility, such as mezzanine flooring, partitioning systems, and security equipment. A well-coordinated setup ensures a smooth and cohesive operational environment.
When working with mezzanine flooring, it's essential to account for load capacity and structural support. The staircase should align perfectly with mezzanine access points without compromising the building's structural integrity - especially in retrofitted spaces where load ratings might vary.
Partitioning systems also need to accommodate the movement of rolling staircases. This means ensuring adequate aisle widths and properly sized access points to avoid interference with unit doors or panels.
Security systems are another crucial consideration. Strategically placed cameras and effective access controls can prevent blind spots caused by staircase movement, safeguarding sensitive areas.
Fire protection and climate control systems must also be factored into the design. Sprinkler systems need to maintain coverage regardless of the staircase's position, and emergency exits must remain clear. Similarly, climate control systems should ensure consistent air circulation around the staircases to maintain stable conditions throughout the facility.
For insights on integrated solutions, explore our Mezzanine Flooring Solutions.
By coordinating these systems, you not only improve daily operations but also simplify maintenance, as outlined below.
Maintenance and Safety Inspections
To keep rolling staircase units operating safely and efficiently over time, regular maintenance and inspections are a must. A proactive maintenance plan not only reduces safety risks but also minimises liabilities for your facility.
Establish a routine that includes daily visual checks, weekly assessments of moving parts, and more in-depth monthly and annual inspections performed by qualified professionals. These steps ensure compliance with safety regulations and manufacturer guidelines.
Annual professional inspections are particularly important. They provide a thorough review of the units, help identify recurring issues, and ensure that your facility meets all safety standards. Keeping detailed records of these inspections also demonstrates compliance and helps streamline future maintenance.
Additionally, having replacement parts readily available minimises downtime and keeps operations running smoothly. Staff training is another key component - ensuring your team knows how to use and maintain the staircases properly further enhances safety and efficiency in the long run.
Conclusion: Improve Your Self-Storage Facility with Rolling Staircase Units
Rolling staircase units are the go-to solution for tackling access challenges and safety concerns in self-storage facilities. These units not only make it easier to reach upper-level storage but also help reduce accidents associated with ladders, making your facility safer for tenants and staff alike.
But the advantages don’t stop there. By allowing additional storage levels without major structural overhauls, rolling staircase units can help you increase your net lettable space - an efficient way to maximise your facility's revenue potential.
PSL takes this a step further with tailor-made designs that align perfectly with your facility's specific needs. From the initial consultation to the final installation, PSL ensures a smooth process and seamless integration with your existing systems. Want to learn more? Check out their Complete Design Services.
"PSL were professional and efficient and it was a pleasure to deal with them. I would recommend PSL as fit out contractors for European storage facilities as nothing was a problem on site and they were extremely helpful throughout the whole job." - Mini Lager, Norway
Investing in rolling staircase units is a smart move for improving operational efficiency, enhancing tenant satisfaction, and reducing liability risks. Whether you’re upgrading an existing facility or planning a new one, these systems are a practical and cost-effective way to expand your storage capabilities.
Looking to take your self-storage facility to the next level? Learn how Rolling Staircase Units for Self Storage Facilities can help you optimise space and improve operations. It's a solution that combines safety and efficiency, setting a higher standard for modern storage facilities.
FAQs
How do rolling staircase units make self-storage facilities safer and more efficient than traditional ladders?
Rolling staircase units provide a safer and more practical solution compared to traditional ladders in self-storage facilities. Unlike ladders, these stairs offer stability and can be easily maneuvered, significantly lowering the chances of falls or injuries when reaching high shelves. Their smooth mobility means staff can relocate them with ease, eliminating the hassle of lifting or shifting heavy equipment.
What’s more, these units are designed with space efficiency in mind. They occupy minimal room and can be neatly stored when not in use, keeping aisles clear and ensuring operations stay organised. With their blend of safety, convenience, and functionality, rolling staircase units have become a smart upgrade for today’s self-storage facilities.
What features make rolling staircase units safe and OSHA-compliant?
Rolling staircase units come equipped with several important features to prioritise safety and meet OSHA standards. These include the capacity to handle at least four times their maximum load, slip-resistant steps and platforms to minimise the chance of falls, and sturdy handrails to provide a secure grip. On top of that, they are built with stability and durability in mind, significantly lowering the risk of tipping or other accidents during use.
These design elements make rolling staircase units a dependable choice for accessing elevated areas across different workplaces.
How can self-storage facilities seamlessly integrate rolling staircase units with mezzanine floors and security systems?
Self-storage facilities can effectively incorporate rolling staircase units with mezzanine floors and security systems by thoughtfully planning access points and ensuring the design works seamlessly with the building's structure. For instance, mezzanine floors should have clearly designated spaces for stair placement, allowing easy and efficient movement between levels.
To improve safety, facilities can extend CCTV monitoring and access control systems to cover staircase areas. It’s also crucial to ensure that the staircase design matches the mezzanine's structural requirements, maintaining stability and adhering to safety regulations.
By tailoring the layout to include secure access points and integrating surveillance and alarm systems with the staircase, facilities can provide a safer and more secure environment for both staff and customers.
Related posts
- 7 Key Features of Modern Self-Storage Facility Design
- 5 Benefits of Locker Storage Units for Your Business
- How External Garage Units Maximise Space in your Self Storage Facility
Design Smarter Facilities with Modular Storage Partition Systems
Modular storage partition systems are transforming how self-storage facilities are designed and built. These systems use pre-made components to divide large spaces into individual storage units, offering a faster, more efficient alternative to conventional construction. Here's why they matter:
- Faster Installation: Off-site fabrication means components can be installed while other site work is ongoing, reducing project timelines by 30–50%.
- Cost Savings: Prefabrication lowers labor costs, reduces waste, and cuts overall construction expenses by up to 30%.
- Flexibility: Easily reconfigure layouts to meet changing customer needs or expand facilities without major renovations.
- Durability: Made from materials like galvanized metal, these systems are built to last with minimal maintenance.
- Customisable Features: Options include solid or mesh partitions, various door styles, integrated shelving, and even climate control for specialised storage.
Key Advantages of Modular Partition Systems
Modular partition systems are transforming facility design by cutting costs and improving efficiency. They're becoming a go-to choice for facility owners who want to get the most out of their investment while staying flexible in their operations. For more details on these solutions, check out our Storage Partition Systems for Self Storage Facilities.
Flexibility and Scalability
One of the standout features of modular systems is their ability to adapt and grow with your needs. Unlike traditional construction, modular partitions can be reconfigured easily as tenant requirements change.
This flexibility is especially useful when market conditions shift. Whether you need to combine smaller units into larger ones or divide spaces into smaller sections, modular systems let you make these changes without the hassle or expense of major renovations.
The scalability of these systems goes beyond simple adjustments. As your business expands, modular components can be moved or repurposed in other parts of your facility. This ensures that your initial investment keeps paying off as your operational needs evolve. Whether you’re optimising your current space or expanding into new buildings, modular systems grow with you.
This adaptability not only supports business growth but also helps you make the most of your available space.
Space Optimisation
Modular partition systems are excellent for getting the most out of every square foot. By strategically placing partitions, you can create units in various sizes to meet the needs of different customer groups and avoid wasted space. This approach allows you to attract a broader customer base and maximise revenue per square foot. Thoughtful layouts also improve accessibility, making it easier for tenants to move their belongings in and out without unnecessary obstacles.
Additionally, modular systems can help you maximise natural light. By using transparent or semi-transparent sections, you can reduce the need for artificial lighting, which lowers energy costs and supports sustainability.
While efficient layouts and space usage boost revenue, the quality of materials ensures these benefits last over time.
Durability and Low Maintenance
The high-quality construction of modular systems is a result of their off-site manufacturing process. Built in controlled environments, these components are precision-engineered to meet exact standards that are hard to achieve with on-site construction.
"When the structure is installed, each piece fits together like a complex puzzle. Because of the attention paid during planning and fabrication, structures built with modular construction are longer‐lasting, requiring much less maintenance on average compared to traditional construction." – STARRCO
This meticulous production process means lower maintenance costs throughout the system's lifespan. Materials like galvanized metal resist corrosion and wear, keeping the structure both sturdy and visually appealing with minimal upkeep.
The financial benefits don’t stop there. Modular construction can cut project timelines by 30 to 50% compared to traditional methods, and prefabrication can save up to 10% on overall construction costs. Plus, these systems may qualify for tax benefits due to faster depreciation schedules.
Another advantage is the reduced waste during manufacturing and installation, which lowers material costs. Combined with fewer on-site labor needs, modular systems are a cost-effective choice for both initial builds and long-term operations. For additional insights, explore our Turn-Key Project Management services.
Designing Facilities with Modular Systems
When planning modular partition systems for self-storage facilities, thoughtful design is essential. A well-planned layout not only optimises functionality but also boosts profitability. Let’s dive into how customisation and technology play key roles in creating effective designs.
Customisation Options
One of the standout features of modular systems is their ability to adapt to various business needs, making them a perfect fit for facilities catering to a wide range of customers. For example, you can design units in different sizes to accommodate everyone, from individuals needing compact storage to businesses requiring larger spaces.
Door styles also offer flexibility. Roll-up doors are ideal for larger units where customers may store bulky items, while swing doors suit smaller, more personal storage spaces. Beyond basic configurations, modular systems can include add-ons like integrated shelving, drawers, and bins. These features help organise stored belongings and even allow operators to charge higher rates for premium storage options.
The use of corrugated metal adds structural strength and supports diverse layouts, making it easier to create different access points and door orientations. This flexibility is particularly useful when dealing with irregularly shaped sites or challenging landscapes.
For operators managing multiple locations, maintaining branding consistency is straightforward with custom color options for metal components. This ensures a cohesive look across all facilities while still tailoring designs to local market preferences.
"Modular storage systems offer a range of benefits for growing businesses, including flexibility, cost‐effectiveness, efficiency, scalability, and future‐proofing." - Midwest Storage Solutions
Want to learn more? Check out our Storage Partition Systems for Self Storage Facilities.
Incorporating Technology
Technology is reshaping how self-storage facilities operate, and modular systems are designed to integrate these advancements seamlessly. For instance, smart entry systems can be built directly into the partitions, eliminating the need for retrofitting and ensuring smooth operation from the start.
Security is another area where technology shines. Modular systems can incorporate individual unit alarms, motion sensors, and access control systems during the design phase, ensuring clean installations and dependable performance.
For specialised storage needs, climate control systems can be integrated into modular designs. Whether it’s HVAC ducting or humidity controls, these additions open up opportunities to serve niche markets like document storage, wine storage, or delicate equipment storage - areas that often command higher rental fees.
Digital monitoring systems are another valuable addition. Sensors for temperature, humidity, and security can be seamlessly embedded into the modular framework, offering comprehensive monitoring without compromising the sleek look of the units. Planning for power and data connectivity during the design phase ensures the facility is ready for future upgrades without the hassle of costly modifications.
Compliance with UK Building Regulations
While customisation and technology are critical, ensuring compliance with UK building regulations is just as important. Modular systems must meet the same stringent standards as traditional construction, including the International Building Code and specific UK regulations.
Structural design reviews are the first step in compliance. Engineers assess designs and specifications to ensure they meet regulatory requirements before manufacturing begins. This proactive approach minimises the risk of costly changes later in the process.
Fire safety is a key concern for self-storage facilities. Modular designs must include fire-resistant materials, proper escape routes, and effective fire suppression systems. Manufacturing in a controlled environment ensures these standards are consistently met.
Accessibility requirements must also be integrated into the design from the beginning. This includes features like wider corridors, accessible unit heights, and user-friendly door hardware. Designing beyond the minimum standards can make facilities more appealing to a broader range of customers.
To ensure full compliance, inspections are conducted at multiple stages - design, pre-delivery, and post-assembly. Engaging engineering and compliance experts early in the process can simplify this journey. For support with design and regulatory adherence, explore our design and compliance services.
Implementation Steps for Modular Storage Systems
Setting up modular storage partition systems requires detailed planning and careful execution. A well-organised approach helps avoid unnecessary delays and expensive adjustments.
Site Survey and Needs Assessment
The first step in any modular storage project is conducting a thorough site survey. This step is essential to identify potential challenges and opportunities before diving into the design process, saving time and money down the road.
Start by collecting crucial documents like land surveys, zoning maps, utility layouts, and existing AutoCAD drawings of the facility. These resources help outline site constraints and possibilities.
During the physical inspection, note key details such as the condition of floors, the placement of columns, lighting systems, fire sprinklers, HVAC ductwork, and clear height measurements. For self-storage facilities, additional attention should be given to dock doors, electrical systems, and any structural elements that could impact partition placement.
The survey also evaluates the specific needs of the facility. For example, will it cater to residential users, businesses, or specialised storage like climate-controlled units? This insight shapes the design to meet customer requirements while considering traffic flow patterns and potential expansion plans.
The result of this process is a comprehensive Site and Survey Layout Report. This document includes detailed measurements, infrastructure mapping, and tailored unit recommendations, serving as the foundation for the design and installation phases.
Using the findings from the survey, you can create a space-maximising layout that aligns with the facility’s goals.
Planning and Layout Design
With the site survey complete, the next step is to transform the data into an actionable plan. This phase focuses on designing layouts that make the most of the available space while ensuring smooth operations.
Start by analysing storage needs and measuring the space available. Designers consider both horizontal and vertical usage, determining where modular components will fit and how they’ll integrate with the current infrastructure.
The goal is to optimise space effectively. Modular systems are particularly good at utilising vertical space and can be configured to meet specific storage needs. Designers group similar unit sizes together, map out high-traffic areas, and address potential bottlenecks to ensure easy customer access.
This phase also involves selecting modular components that are adaptable for future changes. Choices include door styles, partition materials, and additional features like built-in shelving or security systems. The idea is to create a flexible setup that can evolve with business demands.
For facilities requiring specialised storage, such as climate-controlled units, this is the stage to plan for integrating power connections and climate systems. Preparing for these needs upfront avoids costly modifications later.
For more insights into our design process, visit our Complete Design Services page.
Once the layout is finalised, the focus shifts to installation and project management.
Installation and Project Management
The installation phase brings the modular design to life. Professional project management ensures that all activities are coordinated to minimise disruptions and deliver high-quality results. This phase involves manufacturing, delivery, and on-site assembly, all working in harmony.
Early coordination among stakeholders is crucial. Facility owners, engineers, contractors, and materials vendors should collaborate from the beginning. Tools like Building Information Modeling (BIM) software streamline communication and provide real-time updates throughout the project.
The installation process follows a just-in-time delivery approach, ensuring modular components arrive when the site is ready. This minimises the need for on-site storage and reduces the risk of damage to materials.
Inspectors should verify that all components meet design and regulatory standards before they are delivered to the site.
Contingency plans are essential to address potential delays caused by weather, transportation issues, or on-site challenges. These backup strategies help keep the project on schedule, even when unexpected problems arise.
"Manufacturing building components off-site provides for more controlled conditions and allows for improved quality and precision in the fabrication of the component." - National Institute of Standards and Technology and the National Research Council
During installation, extra care is taken to seal and weatherproof the facility. This includes sealing horizontal joints, applying protective membranes, and ensuring vertical connections are watertight.
The final step is system testing and commissioning. This involves checking door mechanisms, security systems, climate control, and any integrated technology to ensure everything works as intended. The project is only considered complete once all components pass testing and receive client approval.
For more information about our modular storage solutions, visit our Storage Partition Systems for Self Storage Facilities page.
sbb-itb-55d1b84
Modular vs Traditional Construction Methods
Understanding the differences between modular and traditional construction can help facility developers make better decisions based on factors like cost, installation time, and long-term adaptability. Below, we break down key distinctions in speed, cost, waste management, design flexibility, and quality control.
Cost, Speed, and Flexibility Comparison
Modular construction significantly reduces project timelines - by as much as 30% to 50% - because off-site fabrication occurs while site preparation is underway. Unlike traditional construction, where tasks happen sequentially, modular construction allows multiple processes to run in parallel.
"Modular construction timelines are often faster than traditional construction timelines, making them more cost-effective." - Marissa Morin, Falcon Structures
The financial benefits of modular construction go beyond just speed. Modular projects typically cost 20% to 30% less per square foot compared to traditional methods. In fact, 65% of building professionals report lower overall project costs with modular systems. Additionally, modular construction is far more efficient in terms of material usage, achieving up to a 90% reduction in waste compared to the overages seen in traditional builds.
When it comes to design, traditional construction offers flexibility throughout the building process, allowing for changes as the project progresses. Modular construction, on the other hand, requires upfront design decisions. However, once installed, modular systems offer unmatched adaptability - they can be reconfigured, expanded, or even relocated with ease. Traditional construction typically involves costly demolition and rebuilding when modifications are needed.
Feature | Modular Construction | Traditional Construction |
---|---|---|
Project Timeline | 30–50% faster completion | Standard construction timeline |
Cost per Square Foot | 20–30% less expensive | Higher upfront costs |
Material Waste | Up to 90% reduction | Significant material overages |
Design Changes | Limited once manufacturing begins | Flexible throughout construction |
Future Modifications | Easy reconfiguration and expansion | Costly demolition and reconstruction |
These advantages make modular construction a popular choice, especially for self-storage facility projects.
Quality Control and Safety
Modular construction also excels in quality control. Manufacturing takes place in a controlled factory environment, eliminating weather-related delays and ensuring consistent quality. This results in higher precision and durability, with structures requiring less maintenance over time.
"Modular allows those coveted skilled workers to remain in fixed locations with controlled and safer conditions as mentioned. Modular plants can be located to attract those competitive workers and take advantage of important access to raw materials and logistic connections, like highways and rail lines, common in other industries, such as automotive and technology products." - Real Projectives
Safety is another key advantage. Since most of the work happens off-site in controlled environments, modular construction reduces safety risks by 80% compared to traditional methods. This safer approach not only protects workers but also contributes to long-term cost savings and operational efficiency.
For self-storage facilities, modular systems are particularly effective. They create standardised, repeatable units that maximise space and keep costs low. However, traditional construction may be a better fit for projects requiring unique architectural designs or integration with existing structures.
Ultimately, the choice between modular and traditional construction depends on your project’s specific needs, timeline, and future plans. Modular systems are ideal for projects that prioritise speed, cost efficiency, and flexibility, while traditional methods are better suited for complex, custom designs. To learn more about modular storage solutions, check out our Storage Partition Systems for Self Storage Facilities page.
Conclusion: Better Storage with Modular Systems
Modular storage partition systems are changing the game for self-storage facility design and construction. These systems make it possible to use space more efficiently, cut down on waste, and expand facilities faster. For businesses embracing modular construction, the advantages translate into real financial gains and a stronger competitive edge.
One of the biggest perks? Modular systems can slash construction costs and cut project timelines in half. This means facilities can start generating revenue much sooner. Considering that the UK alone accounts for 41% of the entire European self-storage market, this speed advantage can have a massive impact on profitability. Faster builds don’t just save money - they set the stage for long-term operational success.
The benefits don’t stop at construction. Modular systems are built for efficiency over time. They’re flexible enough to adapt to changing customer needs, making it easy to reconfigure units or expand in phases without disrupting day-to-day operations. By optimising unit sizes to fit market demands, facilities can maximise rentable space, driving up revenue. As Terry Wellner, CEO of Modular Mini Storage, puts it:
"It is gratifying to help folks new to our industry develop a successful project. They usually wind up with considerably more rentable space than they expected and a much more competitive facility."
Durability is another key factor. Modular systems are designed to last, with reinforced walls, built-in security features, and energy-efficient construction. These qualities keep maintenance costs low while ensuring the facility can handle the demands of modern storage customers.
Perhaps the most powerful feature of modular systems is their ability to grow with ease. Unlike traditional construction, where changes can be a headache, modular systems allow for smooth, non-disruptive updates as market trends shift and customer preferences evolve. This adaptability positions facilities to thrive in an ever-changing industry.
FAQs
How do modular storage partition systems improve flexibility and support growth in self-storage facilities?
Modular storage partition systems offer incredible versatility for self-storage facilities, making it easier to adjust or expand spaces without major construction work. These systems are built to respond quickly to shifting customer needs, helping businesses maximise space usage while staying ready for growth.
Thanks to their customisable designs, modular partitions allow facilities to meet operational demands efficiently, all while keeping disruptions to a minimum during changes. This flexibility not only supports business growth but also boosts efficiency and improves the overall customer experience.
How much time and money can modular construction save compared to traditional building methods?
Modular construction stands out for its time and cost efficiency when compared to traditional building methods. It can cut project timelines by an impressive 25% to 50%, largely due to its streamlined processes and off-site manufacturing. Completing a project faster not only speeds up delivery but also reduces overall expenses.
On the cost side, modular construction often results in savings ranging from 10% to 30%. These savings stem from lower labor costs, minimised material waste, and shorter project durations. For businesses aiming to make the most of their resources, modular construction offers a smart and resource-efficient alternative to conventional building techniques.
How do modular storage systems use advanced technology to enhance security and climate control?
Modular storage systems use cutting-edge technology to offer better security and accurate climate management. With features like automated temperature and humidity control, they ensure a stable environment - perfect for preserving delicate or sensitive items.
On the security side, these systems incorporate tools such as electronic access controls, surveillance cameras, and alarm systems to protect stored items from unauthorised access. This combination of smart features and robust security measures makes modular storage systems a dependable solution for various storage requirements.
Related posts
- 7 Key Features of Modern Self-Storage Facility Design
- How Smart Design Impacts Storage Facility Profits
- Installing Storage Lockers Can Boost Your Strage Facilities Revenue
Installing Storage Lockers Can Boost Your Strage Facilities Revenue
Want to increase your storage facility's revenue without costly expansions? Adding storage lockers to underutilised spaces like basements or parking garages is a quick, efficient solution. Here's why:
- Higher Revenue per Square Foot: Lockers can generate more revenue per square foot.
- Fast ROI: Most facilities recover installation costs in under 12 months.
- Broader Customer Appeal: Compact lockers attract budget-conscious renters, urban residents, and small businesses.
Lockers also reduce operating costs, improve space efficiency, and cater to modern customer preferences like 24/7 access and smart security. Ready to transform wasted space into profit? Keep reading for actionable insights.
Problems with Standard Self-Storage Models
Traditional self-storage facilities face several hurdles that impact both profitability and customer satisfaction. These challenges highlight the need for more modern and efficient storage solutions, which we'll explore in the following sections.
Poor Space Usage
Making the most of every square foot is key to turning unused areas into profit. Unfortunately, traditional storage layouts often leave corners, narrow corridors, and irregular spaces underutilised. This inefficiency is particularly problematic because most households only need small storage spaces, making oversized units impractical and wasteful.
Spaces like basements, awkward corners in parking garages, or other irregular areas often sit idle because they don't fit the standard rectangular unit design. Instead, these areas could be transformed into smaller, more efficient storage locker units, maximising their revenue potential.
Higher Operating Costs
Operational expenses in traditional self-storage facilities can quickly eat into profits, often consuming 30–40% of revenue.
"Given the current inflationary environment and the pressure we're all feeling on our self-storage rental rates, it's important to tighten operating expenses anywhere you can." – Scott Krone, Founder, Coda Management Group
Climate-controlled units further increase utility bills, as larger facilities require more energy for heating, cooling, and lighting. Smaller, more compact storage solutions are far more energy-efficient. Additionally, rising marketing costs put extra strain on smaller operations, underscoring the need to generate more revenue from existing spaces.
Different Customer Needs
Today’s storage customers expect more than what traditional facilities offer. Around 80% of users now prefer contactless rentals with 24/7 access, showing a clear demand for convenience and flexibility. Yet, only 43% of the population is familiar with self-storage services, which suggests that many potential customers find current options either confusing or unsuitable for their needs. This is especially true for those looking for short-term, budget-friendly solutions for seasonal or transitional storage.
"The self-storage market is expected to be dynamic, influenced by economic conditions and shifting demand." – Aaron Sanchez, Managing Director, SkyView Advisors
Modern customers also value tailored experiences and environmentally friendly practices, but most traditional facilities stick to a one-size-fits-all approach. As urbanisation, remote work, and downsizing trends grow, the demand for adaptable storage solutions becomes even more pressing. Meeting these diverse needs is essential for tapping into new revenue streams and staying competitive.
For more tips on improving your storage facility’s performance, check out our PSL Blog.
How Storage Lockers Increase Revenue
Storage lockers turn underutilised spaces into money-making opportunities by addressing the challenges of traditional self-storage models. These compact units not only create new revenue streams but also attract customers who might otherwise overlook conventional storage options.
Better Revenue per Square Foot
When it comes to revenue density, storage lockers outperform traditional self-storage units. Lockers are particularly effective at transforming awkward or irregular spaces into income generators. Unlike larger storage units that require specific layouts, lockers can fit into almost any available space. This flexibility ensures that every square foot contributes to your bottom line.
Additionally, facilities using smart locker systems report earning around £20 more per month per unit. This extra income reflects the value customers place on modern storage solutions that offer improved organisation and accessibility. By increasing revenue per square foot, lockers make it easier to tap into new customer segments.
Higher Pricing Options
Lockers also enable facilities to charge premium rates by offering features that traditional units can’t match. With options like climate control, advanced security, and convenient access, lockers create natural pricing tiers. This allows facilities to cater to both budget-conscious customers and those willing to pay more for extra peace of mind.
Modern storage users prioritise security and control over their belongings. Lockers equipped with integrated monitoring, climate regulation, and advanced access systems meet these demands, giving customers confidence in their choice. This emotional connection often translates into financial gains.
By offering a mix of locker types and sizes, facilities can appeal to a wider audience while maximising occupancy. With the self-storage industry’s average profit margin at 41%, lockers provide an opportunity to surpass this benchmark by attracting customers willing to pay for premium features.
Tiered pricing models also allow customers to choose between basic services or upgraded options, ensuring that facilities capture revenue from a diverse customer base.
For facilities looking to implement locker systems, exploring storage systems can provide the tools needed for steady revenue growth. You can also check out our storage locker unit offerings to find tailored solutions for your business.
sbb-itb-55d1b84
Planning Your Storage Locker Installation
Careful planning can make storage locker installations a smart and profitable investment. The goal is to maximise rentable space while meeting regulations and ensuring the lockers blend smoothly with your facility's existing systems. By focusing on these strategies, you can boost both efficiency and revenue while keeping operations running seamlessly.
Space-Efficient Design
The success of your locker installation starts with understanding how to make the most of your facility's layout. For example, basic drive-up storage typically provides 30% to 35% rentable space, while climate-controlled projects can achieve 40% to 50%. Storage lockers, however, can push those numbers even higher by utilising areas that traditional units might overlook.
Modular locker systems are a great way to adapt to irregular spaces, corners, or unusual dimensions. Unlike fixed storage units, they allow you to make use of every square foot, increasing revenue potential.
When designing the layout, pay close attention to traffic flow. Aisles should be wide enough for two people to walk side by side comfortably, with enough room for customers carrying items. Avoiding dead ends not only improves customer experience but also reduces the risk of vehicle accidents within the facility.
It’s also smart to tailor your unit mix to local demand. Smaller units, like 5-by-10 or 10-by-10 lockers, can be placed at building ends to provide more compact and affordable options. These are especially popular among urban residents and students looking for lower-cost storage solutions.
Phased installations are another option to consider. By planning gradual expansions, you can reduce upfront costs while maintaining operational efficiency. A master plan for the entire property helps ensure smooth traffic flow, proper infrastructure placement, and the flexibility to adapt to market changes.
Security System Integration
A well-thought-out layout is just one piece of the puzzle - integrating advanced security systems is equally important. Strong security measures not only protect the facility but also justify premium rental rates. For example, businesses with access control systems report fewer than five major security incidents per year.
Access control systems are the backbone of secure locker operations. Electronic door locks, paired with keypad or credential-based access, provide much better protection than traditional locks. When integrated with management software, these systems allow for seamless operation and monitoring.
Video surveillance is another key component. About 54% of access control technologies now include video monitoring, which enhances security while lowering operational costs. Place cameras strategically to cover locker areas while respecting customer privacy and adhering to local regulations.
"AWESOME product for self storage owners and managers! We have 9 locations and use SpiderDoor keypads at all of our locations. Our customers love to open the gate and make payments on the SpiderDoor customer app as well."
– Eric Case, Byron Self Storage/Flying Storage Group, GA
Mobile access systems can further improve customer satisfaction. These solutions let tenants manage their accounts, access the facility, and make payments using their smartphones. When paired with a high-quality storage locker unit, these features can justify higher rental rates and improve customer loyalty.
For maximum security, consider a layered approach. Combine physical measures like perimeter alarms and door monitoring systems with ongoing practices like regular security audits. This proactive strategy helps identify and address vulnerabilities before they become problems.
UK Regulation Compliance
Once your design and security are in place, regulatory compliance ensures your investment remains safe and legal. In the UK, storage facilities face strict regulations, particularly after the Grenfell Tower tragedy. The Building Safety Act 2022 and Fire Safety (England) Regulations 2022 have introduced new requirements that significantly impact locker installations.
Fire safety is a top priority. Fire-rated storage systems are essential for containing flames and smoke while maintaining the structural integrity of the building. These systems must meet rigorous standards to comply with regulations.
Building codes also play a role in locker placement, ventilation, and access. Researching local policies on firewalls, sprinklers, and other safety measures is essential, as these rules can influence the overall design. Aligning structures perpendicular to main roads, for instance, can enhance security and allow for easier emergency access.
Ongoing compliance requires regular maintenance and thorough documentation, particularly for fire safety and hazardous materials. The Dangerous Substances and Explosive Atmospheres Regulations 2002 (DSEAR) mandate that risks associated with storing hazardous substances indoors are effectively managed. Your locker systems should address these requirements without compromising operational efficiency.
For those planning large-scale installations, working with professional storage partitioning services can simplify compliance while maximising revenue potential. Professional installation ensures your storage locker unit meets all UK safety standards and makes the best use of available space, setting your facility up for long-term success.
Storage Locker Costs and Return on Investment
Looking into the costs of installing storage lockers shows they can quickly pay for themselves while boosting revenue. Though the upfront expense might appear high, the potential for increased income and a short payback period makes these systems a smart investment.
Installation Costs
The cost of construction varies depending on the type of facility. For single-story structures, expect to pay between £20 and £60 per square foot. Multi-story facilities are pricier, ranging from £40 to £70 per square foot. Additionally, land costs typically make up 20–30% of the total development budget. Other expenses, like site preparation, permits, and the use of high-quality materials, also play a role. However, these initial costs are often quickly offset by the higher rental income generated by locker systems.
Expected Revenue Increases
Storage lockers often bring in more revenue per square foot compared to traditional storage units. For instance, while standard self-storage units usually rent for about £1,20 per square foot, locker systems can command higher rates due to their efficient use of space. On average, self-storage investments deliver annual returns of 8% to 12%, making optimised locker installations a financially appealing option. Operating expenses for these facilities generally range from 30% to 40% of gross rental income, further enhancing profitability. Plus, offering additional services like package acceptance or short-term rentals can open up new revenue streams.
Payback Period
The quick payback period is another strong argument for investing in storage lockers. In many cases, the initial investment is recovered in less than a year. Factors like market demand, dynamic pricing, and operational efficiency all contribute to how fast the costs are recouped. For example, facilities that pair locker systems with modern management tools often enjoy higher occupancy rates and faster rent collection. Partnering with experienced providers who offer end-to-end design services can also help ensure compliance with local regulations and prevent costly mistakes, maximising the return on investment.
Conclusion: Improving Storage Facilities with Lockers
Adding storage lockers to your facility isn’t just about saving space - it’s about creating a smart, revenue-boosting solution that tackles multiple business needs at once.
The financial perks are hard to ignore. Storage lockers help you make the most out of every square foot, increasing revenue while attracting a broader range of customers. Whether it’s e-commerce entrepreneurs looking for inventory storage or businesses needing an affordable alternative to commercial spaces, lockers unlock new opportunities that traditional units might miss.
But the benefits don’t stop there. Lockers can also streamline operations, especially when used as distribution hubs. This added functionality not only improves service for business clients but also boosts profitability by optimising logistics.
Modern locker designs are all about efficiency. They make it possible to serve more customers without needing to expand your facility. And with the self-storage industry averaging profitability margins of around 41%, that efficiency directly translates into higher earnings.
For the best results, it’s essential to work with experienced providers. Partitioning Services Limited has over 24 years of expertise, offering end-to-end solutions across the UK and Europe. From design and manufacturing to installation, they handle it all while ensuring compliance with building regulations. Plus, their custom design options and financing plans make upgrading your facility easier than ever.
Industry experts back this approach:
"A properly planned, operated and funded facility can be a very rewarding and profitable business", says Marc Goodin, Co-founder of Storage Authority Franchising.
With proven returns, broader customer reach, and improved efficiency, installing lockers is a smart investment. When done right, they can turn underutilised spaces into profitable assets that meet the changing needs of today’s market.
FAQs
How do storage lockers compare to traditional storage units in terms of cost and revenue potential?
Storage lockers tend to be a more budget-friendly choice compared to traditional storage units, especially for individuals or businesses with smaller storage needs. Their rental rates are typically much lower, making them a great option for short-term use or those on a tight budget. For instance, while larger storage units might set you back hundreds of dollars each month, lockers are often available at a fraction of that cost.
From a business perspective, offering storage lockers can be a smart way for facility owners to increase revenue. These smaller units appeal to a broader customer base, including those looking for affordable and compact options, which helps improve occupancy rates. Plus, lockers allow for flexible pricing strategies and frequent lease adjustments, giving facility owners more ways to generate consistent income. In short, storage lockers offer an economical solution for users while helping storage facilities boost their bottom line.
How can storage lockers be effectively added to self-storage facilities while ensuring optimal space use and security?
Adding storage lockers to self-storage facilities involves a strategic approach to maximise space and ensure safety. Making the most of your space is crucial - take a close look at your facility’s current layout to find areas where lockers can be added without affecting accessibility or the functionality of existing units. A well-thought-out design can help you serve more customers and boost revenue.
Safety measures are equally important. Incorporate advanced access systems like keypads, card readers, or biometric scanners to control who can enter. Enhance physical security by installing security cameras, improving lighting, and using sturdy fencing. These features not only protect the lockers but also reassure customers that their belongings are safe.
Related posts
- 7 Key Features of Modern Self-Storage Facility Design
- 5 Benefits of Locker Storage Units for Your Business
- How External Garage Units Maximise Space in your Self Storage Facility
How External Garage Units Maximise Space in your Self Storage Facility
Want to boost your self-storage facility's revenue and efficiency? External garage units might be the solution you need.
These units transform unused outdoor spaces into income-generating assets while offering customers convenient, secure, and accessible storage for larger items like RVs, boats, and equipment. Here's why they're a game-changer:
- Better Space Usage: Utilise underused parking lots or outdoor areas to maximise rentable space.
- Convenient Access: Drive-up access simplifies loading and unloading, especially for large or heavy items.
- Higher Revenue: Larger units and premium features justify higher rental rates while attracting a broader customer base.
- Low Maintenance: Durable materials like steel reduce upkeep costs and ensure long-term reliability.
- Cost-Effective Expansion: Build quickly and affordably compared to traditional indoor units, with tax benefits like accelerated depreciation.
External garage units are not just an addition - they're a smart investment to grow your facility's profitability and value. Ready to make the most of your space? Keep reading for a detailed guide.
Benefits of External Garage Units for Self-Storage Facilities
External garage units have reshaped the way self-storage facilities operate by tackling space limitations and opening up fresh revenue opportunities. They offer a smart solution for maximising property usage without the hefty costs of constructing additional indoor buildings.
Better Space Usage
Turning unused outdoor areas into income-generating storage spaces is a practical way for facility owners to expand. Empty land, underutilised parking lots, or perimeter zones can be transformed into valuable assets with well-placed, customisable units.
One of the standout features of these units is their adaptable design. They can be customised to fit specific needs, helping you make the most of your facility's available space. Unlike permanent indoor structures, these external units offer flexibility in size and layout, making them easier to integrate into your property's unique design.
Positioning these units strategically - like near entrances or along driveways - enhances both accessibility and overall space efficiency. This modular setup allows for gradual expansion as demand grows, avoiding the large upfront investment required for traditional building projects.
This combination of adaptability and smart placement not only maximises space but also ensures customers enjoy hassle-free access.
Easier Customer Access
Drive-up access is a game-changer for customers, eliminating the common headaches associated with traditional indoor storage units. The convenience of ground-level access makes loading and unloading items a breeze, especially for large or heavy belongings like furniture, appliances, or business inventory.
For customers who need frequent access, this setup saves time and effort. Business owners, in particular, benefit from the streamlined process of moving goods directly from their vehicle to the unit, reducing physical strain and cutting down on multiple trips through narrow hallways or elevators.
For oversized items - think boats, RVs, or workshop equipment - drive-up access removes the hassle of navigating tight corridors or stairs. This level of convenience makes external garage units an ideal choice for items that indoor units struggle to accommodate.
By making storage easier and more accessible, these units not only improve customer satisfaction but also justify higher rental rates.
Higher Revenue Opportunities
Thanks to their larger size and convenient access, external garage units often command higher rental prices compared to standard storage units. Their versatility allows facilities to expand their service offerings and attract a wider range of customers, boosting overall revenue.
Additionally, offering 24/7 access is a big draw for customers with varying schedules, increasing occupancy rates and enhancing satisfaction. Repurposing vacant land or parking areas into these units is a cost-efficient investment, as it avoids the high overhead typically associated with indoor construction projects.
To learn more about our storage solutions, visit Partitioning Services Limited.
Key Features of External Garage Units
External garage units are designed with specific structural and functional elements to meet the demands of modern self-storage facilities. These purpose-built units combine strength, adaptability, and efficiency, making them a reliable choice for facility operators.
Strong and Secure Construction
At the heart of every dependable external garage unit is its sturdy construction. Built with reinforced steel, these units are designed to endure years of use and stand strong against harsh weather conditions. Unlike wood, which is vulnerable to pests like termites, steel offers unmatched durability and longevity.
The exterior features weather-resistant galvanized steel cladding, which protects against rust and corrosion. This ensures the unit stays in excellent condition over time, safeguarding stored items from moisture, wind, and fluctuating temperatures. Together, these materials create a protective shield, keeping belongings secure.
Security is another critical aspect of these units. Reinforced roller doors and tamper-proof locking systems provide robust protection against unauthorised access. Many units also support the integration of CCTV systems, offering enhanced surveillance for both operators and customers.
The foundation of these units typically includes reinforced concrete slabs, providing excellent load-bearing capabilities and moisture resistance - ideal for storing heavy or bulky items.
For more details on our construction techniques, check out our Partitioning Units page.
Custom Design Options
One of the standout features of external garage storage units is their flexibility in design. These units can be customised to align with specific operational needs, helping facility operators maximise available space and increase revenue.
Their adaptable dimensions make them suitable for a wide range of storage requirements. Whether it’s a compact unit for personal belongings or a larger space for vehicles and commercial equipment, these units can cater to diverse customer needs. This versatility allows operators to attract a broader clientele and charge premium rates for specialised storage options.
PSL offers bespoke design services, enabling operators to customise dimensions, cladding materials, and door placements. These tailored modifications ensure an optimised layout while maintaining a cohesive and professional appearance across the property.
Aesthetic customisations can also be incorporated, such as cladding that matches company branding or colors. This attention to detail reinforces a facility's image, creating a premium look that supports higher rental rates.
"PSL's external garage units can be tailored to meet your specific requirements, helping to maximise the net lettable space within your facility." – PSL Limited
Additional features like insulated roofing, built-in ventilation, and advanced locking systems can also be added during the design phase. These enhancements make it possible to cater to specific storage needs, such as temperature-sensitive or high-value items, providing a tailored solution that combines functionality with durability.
Low Maintenance Requirements
External garage units are designed with long-term efficiency in mind, requiring minimal upkeep and reducing operational costs for facility operators. This low-maintenance design allows operators to focus on growing their business rather than dealing with frequent repairs.
The use of steel and aluminum components ensures resistance to rust, pests, and storm damage, significantly lowering maintenance expenses. Galvanized steel coatings provide an additional layer of protection against environmental wear, extending the lifespan of the units far beyond that of traditional materials like wood. Unlike wooden structures, which require regular painting, sealing, and pest treatments, these units maintain their appearance and performance with minimal intervention.
With durable materials, weather-resistant finishes, and solid construction, these units deliver reliable service for decades, making them a cost-effective choice for operators aiming to maximise their return on investment.
For more information on efficient and cost-effective solutions, visit our Turn-Key Project Management page.
Adding Garage Units to Your Current Facility
Expanding your self-storage facility with external garage units requires thoughtful planning. It’s not just about placing units on unused land - it’s about optimising space, managing traffic flow, and adhering to regulations to ensure smooth operations and a positive customer experience.
By carefully following these steps, you can transform your facility into a more efficient and profitable operation.
Planning Layout and Traffic Flow
The layout of your garage units plays a critical role in ensuring smooth operations and customer convenience. Proper positioning optimises space while allowing vehicles to move easily and safely through the facility.
When designing the entrance and exit points, consider the variety of vehicles customers bring - ranging from compact cars to large moving trucks. To accommodate this, main drive aisles and fire lanes should be at least 30 feet wide, while secondary aisles should measure between 20 and 24 feet. This ensures two-way traffic flows smoothly and emergency access is never compromised.
For facilities with a single entry and exit point, a looped drive design can prevent the need for customers to reverse or navigate tight turns. However, if dead-end aisles are unavoidable, make sure there’s sufficient turnaround space to avoid traffic jams.
For facilities offering boat and RV storage, wider aisles are essential. In these areas, drive aisles should be 15 feet wider than the depth of the storage units, allowing for easier maneuvering. Placing boat and RV units across from each other can also reduce the amount of paving required while maximising space efficiency.
Strategically placing garage units along the facility’s perimeter can serve a dual purpose. These single-sided, inward-facing units not only maximise the use of boundary areas but can also act as a security barrier. Additionally, positioning units on both sides of an aisle minimises paving costs and increases revenue per square foot.
With a well-thought-out traffic flow and layout, the focus shifts to converting unused outdoor areas into productive storage spaces.
Converting Unused Outdoor Areas
Turning underutilised outdoor spaces into revenue-generating storage areas can significantly boost your facility’s profitability. Many self-storage facilities have vacant land or underused parking areas that can be repurposed with proper planning.
To make the most of these spaces, prioritise layouts that maximise rentable square footage while minimising non-revenue areas like offices or wide corridors. For instance, banks of units should be no narrower than 20 feet to maintain structural integrity and cost efficiency.
Convenience for customers is key during this process. Make sure units are easy to access with minimal turns from main entry points. Perimeter areas often offer the easiest conversion opportunities, as they require fewer modifications and provide direct vehicle access - an important factor for garage storage units. Additionally, these conversions can often be completed without disrupting the operation of existing units, allowing you to continue generating revenue during the expansion.
Once the conversion is complete, it’s crucial to ensure your facility meets all safety and building standards.
Meeting Safety and Building Requirements
Every expansion or conversion project must comply with local safety and building regulations. From fire safety codes to accessibility standards, adhering to these requirements is essential for legal and operational success.
Before construction begins, check if planning permission is necessary - especially for detached garage units or changes that might alter the facility’s appearance. Submit a building notice or full plans application to your local building control office to ensure all required standards are met.
Electrical work must align with current wiring regulations and be performed by qualified professionals. For facilities storing vehicles or equipment containing flammable materials, compliance with Dangerous Substances and Explosive Atmospheres Regulations 2002 (DSEAR) is critical. This includes proper ventilation and fire suppression systems to ensure safety.
In many cases, outbuildings are considered permitted development and may not require planning permission. However, this depends on factors like size, height, proximity to boundaries, and location relative to the main building. Keep in mind that these allowances don’t apply to flats, maisonettes, or properties with existing planning restrictions.
Partnering with experienced professionals can simplify the approval process. For instance, PSL’s Turn-Key Project Management services handle everything from compliance to construction, ensuring your project stays on track while avoiding unnecessary delays.
sbb-itb-55d1b84
Financial Benefits and Return on Investment
Beyond operational perks, the financial upsides make external garage units an appealing investment. Lower upfront costs, higher rental income, and increased property value all contribute to a solid business case for expansion.
Lower Construction Costs
External garage units are more cost-effective to build than traditional indoor storage facilities, offering comparable capacity at a fraction of the expense. They don’t need extensive HVAC systems, interior lighting, or complex fire suppression, which also means faster construction and quicker revenue generation.
The savings don’t stop there. Under U.S. tax regulations, external garage units often qualify for favorable tax incentives. Through cost segregation studies, facility owners can accelerate depreciation on qualifying assets, saving on taxes during the early operational years. For example, storage units may be classified as "tangible personal property", allowing depreciation over seven years instead of the standard 39 years for commercial buildings. Some components, like interior partitions, may even qualify for five-year depreciation.
Premium Rental Income
External garage units command higher rental rates, especially for vehicle storage. Their larger size and convenient drive-up access justify premium pricing, boosting revenue per square foot. These units are popular with a wide range of customers, including contractors storing equipment, RV owners needing seasonal parking, and small business owners seeking accessible inventory storage. With approximately 124 square feet of rental space, these units cater to customers who need more room than standard storage options provide. Enhanced security features further support premium pricing, making them a valuable addition to any facility.
For more storage solutions and design inspiration, check out our garage storage units.
Increased Property Value
Adding external garage units can significantly increase your property’s market value while giving you a competitive edge in the local storage market. The additional revenue streams and expanded customer base make your property more appealing to buyers and lenders. High-quality external structures can boost property value by about 1–2%.
The self-storage industry’s steady growth - exceeding 7% annually, with facilities operating at roughly 90% capacity - highlights the long-term advantages of offering diverse storage options. Strategically placing these units, such as along facility perimeters, not only generates income but also enhances security, ensuring that every square foot contributes to profitability.
With their combination of lower construction costs, premium rental income, and increased property value, external garage units offer a strong return on investment. These units typically pay for themselves within the first few years and continue to deliver consistent cash flow throughout their lifespan.
Discover more about our services at Partitioning Services Limited.
Conclusion: Expanding Your Storage Facility with External Garage Units
External garage units offer an excellent way to turn unused outdoor areas into a steady source of income. They combine affordability with high earning potential while providing secure and convenient storage options. This approach not only boosts your current revenue but also increases the long-term value of your property. These units can be seamlessly incorporated into your existing facility, ensuring no space goes to waste.
You can customise these units to fit specific dimensions, integrate them with your current security systems, and match their design to your facility's overall look. Whether you’re repurposing empty parking spaces or expanding along the edges of your property, external garage units offer the flexibility to optimise every inch of available space.
"PSL offers bespoke design, cost-effective solutions, and high-quality construction. Our units are designed to be clean, dry, and insulated, providing an optimal storage environment. Our commitment to quality and customer satisfaction ensures that your storage facility will stand out in the market." – PSL
Built to last, these units feature weather-resistant cladding and durable roller shutter doors, making them capable of withstanding tough conditions while keeping maintenance needs low. Their durability ensures consistent performance throughout their lifespan.
For facility owners looking to expand and attract more customers, external garage units are a practical solution. With features like 24/7 accessibility, enhanced security, and premium storage spaces, they represent a solid investment that supports both immediate and long-term profitability.
As the self-storage industry continues to grow, facilities that offer a variety of storage options are better equipped to stay competitive. External garage units are more than just an addition - they’re a forward-thinking investment in your facility’s future success.
Explore how our garage storage units can elevate your facility, and check out our complete design services to expand your self-storage offerings even further.
FAQs
What are the cost and maintenance differences between external garage units and traditional indoor storage units?
External garage units tend to be a more budget-friendly choice compared to indoor storage units. The key reason? They usually don’t include features like climate control, which keeps their rental costs lower. For those watching their wallets, this can be a big plus.
When it comes to upkeep, external garage units are generally easier to handle. Unlike indoor units, which often need frequent checks for climate systems and extra security measures, external units are fairly straightforward. Once set up, they only require occasional maintenance, making them a practical, low-hassle option for a variety of storage needs.
How can external garage units optimise space in a self-storage facility?
Integrating external garage units into a self-storage facility can boost both its functionality and storage capacity. However, proper planning is vital to ensure the new units blend seamlessly with the existing layout. One key factor is maintaining smooth traffic flow - customers should have plenty of room to load and unload their belongings without hassle. Adequate space for vehicles to maneuver is a must.
It’s also important to focus on structural considerations and accessibility. The units should meet local building codes, have proper drainage systems to prevent water damage, and include ventilation to protect stored items from humidity or other environmental factors. On top of that, don’t overlook security - features like gated access and surveillance systems can go a long way in building customer trust and ensuring safety.
Finally, take the time to evaluate local storage demand. By understanding what customers in the area need, you can determine the right number and sizes of units to add, ensuring your investment aligns with both customer preferences and revenue goals.
How do external garage units improve security and accessibility in self-storage facilities?
Why External Garage Units Are a Smart Choice
External garage units bring together better security and convenience, making them a valuable feature for self-storage facilities. These units are often equipped with top-notch security features like surveillance cameras, gated entry systems, and individual alarms for each unit. These measures work together to keep stored belongings safe from theft or unauthorised access.
On top of that, these units typically offer drive-up access, allowing customers to load and unload their items directly from their vehicles. This setup is especially helpful for moving larger or heavier items, saving both time and effort.
With their combination of strong security and easy accessibility, external garage units are a practical option that caters to customer needs while enhancing the overall functionality of self-storage facilities.
Related posts
- 5 Benefits of Locker Storage Units for Your Business
- How Smart Design Impacts Storage Facility Profits
- Design Smarter Facilities with Modular Storage Partition Systems
How Smart Design Impacts Storage Facility Profits
Want to increase storage facility profits? Start with smarter design. Here's how:
- Optimise Space: Facilities with better layouts achieve 96.5% occupancy and 70% net operating income (NOI). Multi-level designs and flexible unit systems maximise rentable areas.
- Add Climate-Controlled Units: These rent for 20–50% more
- Enhance Security & Accessibility: Advanced security systems lower costs and justify premium pricing. Customer-friendly layouts improve satisfaction and retention.
- Invest in Technology: Smart climate controls reduce energy use, while CAD tools prevent costly design errors.
Quick Tip: Facilities with poor design can lose up to 10% in rental income due to mismatched unit sizes or inadequate climate control. Fixing these issues can significantly boost revenue and customer satisfaction.
Want to know more about avoiding common design pitfalls and increasing profitability? Read on.
Common Design Problems in Storage Facilities
Poor design decisions in storage facilities can directly hurt profitability, leading to lower occupancy rates and reduced revenue. To make the most of your investment, it’s essential to recognise some of the most frequent design mistakes. These issues typically fall into three main categories: space utilisation, operational efficiency, and financial impact. Let’s break down how these problems can affect your bottom line.
Poor Space Usage
One of the biggest mistakes in storage facility design is inefficient use of space. When unit sizes don’t align with what customers need, you risk wasting valuable rentable areas. For example, larger units may fill up space but often generate less revenue per square foot compared to smaller, well-proportioned units that match market demand. On the other hand, smaller units - when sized strategically - can bring in more profit. Incorporating multi-level layouts can also boost revenue density, but only if executed properly.
Daily Operation Challenges
Operational inefficiencies caused by poor design can disrupt both staff workflows and customer experiences. For instance, a 24-foot aisle width allows for smooth two-way traffic, while a driveway with a 45-foot turning radius (instead of the standard 25 feet) can better accommodate larger moving vans. Without these considerations, access becomes more difficult, creating safety risks and logistical headaches. These operational flaws not only frustrate customers but also add to the financial strain caused by design missteps.
Cost Impact of Design Flaws
Design oversights can have significant financial consequences. Here’s a closer look at how specific flaws can hurt profitability:
Design Flaw | Financial Impact | Additional Consequences |
---|---|---|
Poor Unit Mix | Up to 10% lower rental rates | Higher vacancy rates in mismatched units |
Inadequate Climate Control | 20-50% reduced potential revenue | Increased maintenance costs |
Insufficient Security Measures | £7-12 per square foot lower rental rates | Higher insurance premiums |
Beyond these examples, other factors like poor environmental planning and maintenance issues can further eat into profits. For instance, facilities with more than 10% of accounts receivable tied up in overdue payments might be compensating for deeper design flaws, such as filling units with unreliable tenants.
For expert advice on improving your facility’s design and operational efficiency, visit our PSL homepage.
Design Solutions That Increase Revenue
A well-thought-out design can significantly boost revenue by maximising available space and attracting higher rental rates. Below, we explore how flexible layouts, multi-level facilities, and market-driven unit mixes address common challenges and unlock greater profitability.
Adjustable Unit Systems
Flexible partitioning systems allow storage facilities to adapt to changing market demands, making the most of the available space. For instance, a self storage building layout with movable walls can be reconfigured on demand. Imagine turning a single 300 sq ft unit into three 100 sq ft units during peak moving season. This approach not only meets customer needs but also increases revenue per square foot by offering a more optimised unit mix.
Multi-Level Storage Options
Taking flexibility a step further, multi-level designs make it possible to maximise rentable space without expanding the building's footprint. Modern facilities achieve this by strategically placing elevators and optimising traffic flow. Here's how multi-level storage impacts revenue:
Feature | Revenue Impact | Additional Benefits |
---|---|---|
Three-Story Design | £42–70 per sq ft | Lowers fire-rating costs |
Narrow Aisle System | Up to 50% more storage | Enhances space efficiency |
Strategic Elevator Placement | Optimised space utility | Improves accessibility |
Market-Based Unit Mix
Understanding market trends is essential for designing a unit mix that meets demand. As noted by Mordon Intelligence:
"The increasing rate of urbanisation is one of the significant factors positively driving market growth. The rising urban population means smaller and increasingly expensive living spaces in cities with more renters who move frequently."
To align with these trends, consider the following strategies:
- Tailor unit sizes to local demographics.
- Maintain a 75/25 split between residential and commercial units.
- Focus on high-demand sizes, such as 10×15 and 10×20 units.
- Regularly analyse occupancy data to fine-tune the unit mix.
Facilities that align their unit offerings with market demands often achieve occupancy rates exceeding 90%, while commanding premium rental rates. Up next, we’ll delve into how modern technology systems can further enhance profitability.
Tech Systems That Improve Profits
Incorporating advanced technology not only cuts costs but also enhances customer experience and security, creating a win-win for businesses.
Modern Security Systems
Upgrading to modern security systems can significantly lower expenses while fostering trust. Industry data shows that surveillance cameras can slash security costs by up to 75% compared to relying solely on traditional guard services. By integrating cameras, access control, and alarms into a cohesive system, businesses can deter crime and safeguard assets, reducing dependence on on-site personnel.
"Investing in advanced security systems - such as cameras, access control, and alarms - helps storage facilities prevent crime, protect valuables, and build long-term business success", says Hailee Gardner, Marketing Writer at LVT.
A prime example is the Eagle Eye Network, which provides features like real-time monitoring, smart video search, and license plate recognition, ensuring quick and effective responses to potential threats.
Smart Climate Control
Smart climate control systems are a game-changer for reducing costs and increasing revenue. Climate-controlled units typically command rental rates that are 15–35% higher than standard units. These systems also lower energy consumption through automated temperature management, leading to reduced utility bills, less frequent maintenance thanks to predictive monitoring, and an extended lifespan for facilities.
"Investing in climate control not only protects your self-storage customers' belongings, it enhances facility value, efficiency and long-term profitability", explains Bailey Corns, Writer at Evergreen Heating & Cooling.
Computer-Aided Design Tools
Using Computer-Aided Design (CAD) tools to plan a self-storage building layout can maximise revenue potential before construction even begins. These tools streamline space optimisation, identify inefficiencies, and minimise costly design errors. Modern CAD systems offer real-time 3D visualisations, precise measurements, seamless integration with management software, and automated compliance checks. Considering that operational costs make up over 30% of annual expenses, efficient design is essential for profitability.
sbb-itb-55d1b84
Design Features That Keep Customers
Customer-focused design isn't just about appearances - it's a game-changer for satisfaction and retention. At Partitioning Services Limited, we specialise in turning ordinary storage facilities into spaces that customers value, helping you charge premium rates while keeping them coming back.
Easy Navigation Design
Nobody likes getting lost, especially when they're in a hurry. A well-thought-out layout can eliminate common navigation headaches for customers. For example, maintaining 23-28 feet of space between buildings (or 35 feet in snowy regions) ensures smooth traffic flow.
To make navigation effortless, consider these key elements:
- Perpendicular building alignment to main roads for better visibility.
- Clear sightlines between structures to deter unwanted activities.
- Directional signage strategically placed at decision points.
- Well-lit corridors paired with easy-to-follow wayfinding systems.
When customers can find their way around easily, it’s not just convenient - it’s a reason for them to stay loyal.
Better Access Points
Streamlined access doesn’t just make things easier; it also boosts security. Our self storage building layout experts recommend integrating advanced access technologies that enhance both convenience and safety.
Feature | Benefit | Revenue Impact |
---|---|---|
Digital Keypads | Secure entry any time, day or night. | Drives higher occupancy rates. |
App-Based Access | Contactless and user-friendly. | Lets you charge premium prices. |
Real-Time Monitoring | Keeps the facility secure. | Cuts down on insurance costs. |
Motion-Activated Lighting | Safer, well-lit spaces. | Reduces operating expenses. |
With these systems in place, customers feel safer and more in control - two things that are key to keeping them satisfied.
Visual Appeal Impact
First impressions matter, and a visually appealing facility can justify higher rates. Here’s how you can make your space stand out:
- Incorporate modern architectural elements that convey quality.
- Use brand colors to reinforce identity and professionalism.
- Maintain landscaped areas to create a welcoming atmosphere.
- Install professional signage to build trust and credibility.
When these design features are combined with intuitive layouts and advanced tech, they create a seamless experience that keeps customers happy - and your business thriving.
Steps to Implement Better Design
Revamping your storage facility isn't just about making it look better - it's about creating functional spaces that improve efficiency and profitability. By focusing on strategic updates and meeting modern standards, you can ensure your facility stays competitive while driving revenue growth.
Meeting Safety Standards
Safety compliance goes beyond ticking boxes - it’s about fostering trust and ensuring a secure environment for your staff and customers. High-pile storage facilities, in particular, require specific fire safety measures.
Key safety features to prioritise:
- Sprinkler Systems: Ensure a 36-inch clearance from the tops of stored items.
- Fire Suppression: Invest in modern fire prevention systems.
- Access Control: Use digital systems to manage and monitor entry points.
- Emergency Preparedness: Maintain clear signage and conduct regular safety drills.
"Warehouse compliance is a critical cornerstone for ensuring the seamless functioning of operations while adhering to established regulations and prioritising the safety of workers." - Element Logic Insights
Tracking Design Success
To make sure your design improvements are worth the investment, it’s essential to measure their impact. Keep an eye on key performance indicators (KPIs) to evaluate success and pinpoint areas for further improvement.
Performance Area | Key Metrics |
---|---|
Space Utilisation | Storage productivity |
Operational Efficiency | Put-away cycle time |
Customer Satisfaction | Order accuracy |
Safety Performance | Incident rate |
Remember, operating expenses like real estate taxes and management costs are significant, so smart design choices can make a big difference. Tracking these metrics will help confirm your design changes are contributing to the overall success of your facility.
For more ideas on how to optimise your facility’s design, check out our comprehensive design solutions page.
Conclusion: Design's Role in Storage Profits
Data reveals that well-planned layouts can achieve occupancy rates of up to 96.5% and generate a 70% net operating income (NOI). With the self-storage market expected to grow, the role of strategic design has never been more crucial.
Successful facilities harness design to optimise space, enhance customer satisfaction, and boost operational efficiency. Here's how:
Design Element | Impact on Profitability |
---|---|
Space Optimisation | Maximises rentable square footage, with modern facilities averaging 546 units. |
Customer Experience | Improves retention by offering better accessibility and convenience. |
Operational Efficiency | Lowers costs through smart technology and energy-saving systems. |
Modern designs not only improve functionality but also allow facilities to charge premium rates. In the UK, facilities saw an average rental return rise of approx £20 per square foot over the past year. Multi-story layouts, especially in urban areas, are proving to be a smart way to maximise space and meet increasing demand. These shifts underscore the importance of evolving designs to stay competitive.
"In the rapidly growing self-storage industry, good design is key to success. From maximising space and improving customer experience to ensuring security and sustainability, the design of a facility has a direct impact on its profitability." – Janus International
Looking ahead, facilities must embrace layouts that reflect emerging trends like flex-office spaces and improved street-level aesthetics. To explore how design can transform your facility, check out our self-storage building layout and complete design services. With the industry poised to grow another 8.1% by 2025, investing in thoughtful design is the key to thriving in an increasingly competitive market.
FAQs
How do multi-level designs and flexible unit layouts boost storage facility profits?
Multi-level designs and adaptable unit layouts play a key role in boosting the profitability of storage facilities. By building upward, multi-level facilities make the most of limited land space, packing in more storage units without needing to expand the property. This means more tenants can be accommodated within the same footprint, leading to higher rental income.
On the other hand, flexible unit layouts allow storage facilities to adjust to shifting customer needs. Units can be reconfigured to offer different sizes or features, like climate-controlled options, based on demand. This adaptability not only broadens the appeal to a wider customer base but also helps facilities stay aligned with market trends, ensuring a steady stream of income over time.
What are the most common design mistakes in storage facilities that reduce profits, and how can they be fixed?
Design errors in storage facilities can take a serious toll on profitability. Common culprits include off-target unit mixes, poorly designed layouts, and lacking security measures. For instance, offering the wrong blend of unit sizes can leave valuable space sitting idle, while a confusing layout might frustrate customers and make the facility less appealing. On top of that, weak security can deter potential tenants, driving down occupancy rates.
To tackle these challenges, facility owners should start with detailed market research to pinpoint the unit sizes and configurations that best suit their target customers. It's equally important to focus on smart layouts that maximise space and make navigation easy for users. Lastly, upgrading to reliable, top-tier security systems can help attract tenants and keep them coming back, boosting both trust and long-term profitability.
How can smart technology, like climate control and advanced security systems, boost profits for storage facilities?
Investing in smart technology like climate control and advanced security systems can play a big role in boosting profits for storage facilities. These upgrades not only improve operational efficiency but also enhance the overall customer experience.
Take climate-controlled units, for example. They protect sensitive items from damage caused by extreme temperatures or humidity. Customers value this protection and are often willing to pay higher fees for it, which can lead to higher occupancy rates and increased revenue.
On the security side, modern systems such as surveillance cameras and smart locks add an extra layer of safety. They also give tenants peace of mind, building trust and encouraging longer rental periods. At the same time, automation helps cut costs by simplifying processes and reducing the need for on-site staff, freeing up resources for other priorities.
Altogether, these tech upgrades create a high-end experience that helps storage facilities stand out while driving profitability.
Related posts
- 5 Benefits of Locker Storage Units for Your Business
- Installing Storage Lockers Can Boost Your Strage Facilities Revenue
- Level Up Access and Safety with Rolling Staircase Units
Why Outsourcing Storage Facility Management Makes Sense
Managing a self-storage facility can be overwhelming, but outsourcing makes it easier and more efficient. Here's why it works:
- Save Time and Reduce Stress: Professionals handle daily tasks like marketing, security, and maintenance, so you can focus on growth.
- Lower Costs: Outsourcing cuts expenses like employee training, emergency repairs, and insurance premiums.
- Stay Compliant: Experts ensure your facility meets health, safety, and data protection regulations.
- Boost Performance: Advanced technology, better customer service, and proactive maintenance improve occupancy rates and profits.
- Simplify Growth: Scale your business effortlessly with flexible, expert support.
Quick Comparison:
Aspect | Self-Managed Facilities | Professional Management |
---|---|---|
Operating Costs | Higher due to staffing/training | Lower via economies of scale |
Risk Management | Limited expertise | Expert oversight |
Technology Integration | Basic systems | Advanced, regularly updated |
Compliance | Time-consuming | Handled by experts |
Customer Service | Limited | Dedicated, enhanced support |
Maintenance | Reactive | Proactive and efficient |
Outsourcing your storage facility management isn’t just about convenience - it’s about unlocking long-term growth and profitability.
Common Problems with Self-Managed Storage Facilities
Running a storage facility in-house often creates hurdles that impact both efficiency and profitability. Let’s break down some of the most common challenges.
Daily Management Tasks
Owners of self-managed storage facilities face a laundry list of responsibilities, including:
- Marketing to attract customers
- Monitoring security systems and performing maintenance
- Hiring, training, and managing employees
- Standardising and enforcing policies
- Managing software and hardware systems
- Collecting rent and handling financial reporting
"Storage facility maintenance requires you to complete a huge number of tasks spread out over a long period of time - without a way to keep track, you're going to forget things and double up on tasks."
These scattered responsibilities can quickly become overwhelming. That’s where our third-party self-storage management service steps in, streamlining operations so you can shift your focus to growing your business.
Hidden Costs
Managing daily operations is just the tip of the iceberg. Hidden costs often eat into profits, including:
- Emergency repairs and maintenance
- High employee turnover and ongoing training expenses
- Rising insurance premiums
- Unpredictable utility bills
- Frequent adjustments to marketing campaigns
These expenses can add up fast, creating financial strain that’s hard to manage without expert guidance.
Barriers to Business Growth
As costs rise and internal resources are stretched thin, expanding the business becomes increasingly difficult. Common roadblocks include:
- Lack of advanced analytics for strategic decision-making
- Ineffective pricing strategies
- Variability in the quality of service provided
"Self storage performance depends on an operator's ability to attract new tenants - often with teaser rates and discounts - and then impose existing customer rent increases (ECRIs), which can exceed 10% per year. The best operators employ advanced data analytics around customer behavior to optimise discounts and teaser rents against long-term client retention and income growth." - John Affleck, Senior Director – Americas Research, CBRE Investment Management
Without access to professional expertise, many facilities fall short of the industry’s average 41% profit margin. Partnering with a Turn Key Self Storage Facility Management service can help overcome these challenges and unlock the potential for sustainable growth.
Benefits of Professional Storage Management
Professional storage management offers a range of advantages that help facility owners get the most out of their investment while reducing day-to-day challenges. Here’s why outsourcing can be a smart move.
Reduced Operating Costs
Using professional storage solutions is an effective way to cut costs without sacrificing service quality.
Instead of hiring a full-time logistics manager, which can cost around £60,000 annually, facilities can rely on expert management for a predictable monthly fee. This approach helps streamline expenses and maintain control over budgets.
Key cost-saving areas include:
- Lower equipment and maintenance costs
- Reduced insurance premiums through better risk management
- Optimised utility usage
- Vendor relationship savings ranging from 10%-20%
Professional Compliance Management
Staying compliant with regulations is critical, and third-party self-storage management ensures facilities meet all necessary standards. This includes managing:
- Health and safety regulations
- Fire Safety Act 2021 mandates
- GDPR data protection requirements
- Building Safety Act 2022 guidelines
By addressing compliance proactively, facilities can avoid hefty fines, which average around £150,000, protecting both owners and tenants from legal and financial risks.
Flexible Growth Options
Professional management also supports facilities in scaling operations to match market demands. This adaptability is especially useful during seasonal peaks or when planning expansions. Hybrid solutions, which combine remote technology and on-site expertise, make scaling even more efficient.
Scalability advantages include:
- Adjusting service levels quickly to meet demand
- Accessing resources and expertise for expansion
- Lowering risks when entering new markets
- Incorporating advanced technology to boost productivity
These advantages highlight the value of outsourcing, setting the stage for a deeper look at self-managed versus professionally managed storage facilities.
Full-Service Storage Management Solutions
Managing modern storage facilities requires a well-thought-out plan that's executed with precision and supported over time. This is the foundation of our Turn Key Self Storage Facility Management approach, which encompasses everything from design and construction to day-to-day operations.
Space Planning
Making the most of every square foot is key. Our efficient designs focus on:
- Smart layouts using AutoCAD and thoughtful traffic flow strategies
- Compliance with accessibility standards and optimised loading zones
- Climate-controlled areas tailored to local demand
- Unit configurations that align with market needs
Construction and Setup
Building a storage facility is all about coordination and attention to detail. With third-party self storage management services, you get:
- Full compliance with building regulations
- Installation of fire safety systems
- Advanced security system setup
- Climate control systems tailored to the facility
- Mezzanine floors for additional storage space
Once the facility is up and running, ongoing management ensures everything continues to operate smoothly and efficiently.
Ongoing Management Services
To keep your facility performing at its best, professional management services cover all the bases:
Service Category | Key Components | Impact |
---|---|---|
Maintenance | Preventative scheduling, equipment servicing | Extends asset lifespan by 33% |
Customer Systems | CRM tools, payment processing | Boosts revenue by 21–30% |
Operational Support | Security monitoring, climate control | Increases conversion rates by 10%+ |
Financial Management | Invoice tracking, revenue management | Cuts down on late payments |
This structured approach ensures long-term success and smooth operations.
"Our approach emphasizes operational excellence and exceptional customer service", says Storage Asset Management.
In addition, advanced software solutions and eco-friendly features like LED lighting and smart climate controls help reduce costs while improving efficiency. These combined efforts are what make our Turn Key Self Storage Facility Management service stand out.
sbb-itb-55d1b84
Self-Managed vs Professional Management
Let's delve deeper into the key differences between self-management and professional management for storage facilities. Your decision here can significantly influence both operational efficiency and overall costs.
Here’s a quick comparison of the two approaches:
Aspect | Self-Managed Facilities | Professional Management |
---|---|---|
Operating Costs | Higher overhead due to staffing, training, and software expenses | Lower costs thanks to economies of scale |
Risk Management | Limited expertise, leading to higher liability risks | Expert risk management with liability often shifted to the provider |
Technology Integration | Basic systems with infrequent updates | Advanced systems with regular updates and improved functionality |
Compliance | Requires time-intensive internal monitoring | Professionally managed compliance with continuous updates |
Customer Service | Limited hours and minimal support | Dedicated teams offering enhanced service and availability |
Maintenance | Reactive and often delayed | Proactive scheduling with quick issue resolution |
This table highlights how professional management often leads to smoother operations and better results.
Sarah Stapley, an expert in the field, puts it best:
"Outsourcing allows you to scale your services up or down as needed without having to worry about hiring or eliminating staff. This can be particularly useful in a self-storage operation, where demand can fluctuate seasonally or due to other factors."
Recent events also underscore the risks tied to self-management. For instance, one self-managed storage facility faced over 200 break-ins in April alone. Situations like these emphasize the importance of professional oversight to safeguard both your assets and your reputation.
Industry experts often warn against underestimating the complexities of self-management:
"Many people look at the self-storage industry from afar and say, 'Now that's an easy venture.' It isn't true."
Our storage facility solutions provide comprehensive management services, covering everything from operations and finances to marketing and maintenance. Curious about outsourcing options? Check out our third-party self-storage management services for more details.
Steps to Outsource Storage Management
Switching to professional storage management requires careful preparation. Here's a step-by-step guide to help you make the transition smoothly.
Selecting a Management Company
When choosing a storage management partner, look for key qualities that ensure efficient operations and customer satisfaction:
- Proven industry experience in self-storage management
- A wide range of services, including maintenance, customer support, and detailed reporting
- Advanced technology integration for facility monitoring and customer management
- A strong focus on staff training and delivering excellent customer service
Our storage facility solutions cover all these bases, offering comprehensive management services. Once you've chosen the right partner, set clear goals to guide the collaboration effectively.
Setting Management Goals
Defining clear objectives is essential to building a productive outsourcing relationship. As Adelina Bikeneeva from Premier NX points out:
"The establishment of clear expectations can and must be accomplished through a well-drafted, clear, realistic and experience-driven SLA as well as frequent contact with your provider to ensure that these expectations are being fulfilled as the project is executed."
Here are some measurable goals to focus on for your Turn Key facility:
- Maximising occupancy rates
- Steady and consistent revenue growth
- Delivering excellent customer satisfaction
- Ensuring timely maintenance and issue resolution
Performance Monitoring
Once your goals are in place, it's crucial to implement systems that track and measure performance. Regular monitoring ensures your facility operates efficiently. As Peter Abualzolof of Mashvisor advises:
"Outsourced developers should be evaluated in the same way as full-time talent, and the most straightforward way to measure their performance is through velocity, expressed in story points."
Our third party self storage management services include tools and strategies to keep your facility running at its best:
- Daily tracking of performance metrics
- Real-time monitoring of occupancy levels
- Detailed financial reporting
- Collecting and analising customer feedback
- Scheduling and tracking maintenance tasks
Regular reviews help pinpoint areas for improvement and maintain high standards. Typically, management fees range from 5% to 7% of gross income, with minimum monthly fees between £1,500 and £3,000 per property. With consistent oversight, professional management can significantly enhance your facility's long-term success.
Conclusion
Effective storage facility management plays a key role in driving growth and improving operational efficiency. With the self-storage industry on track to hit £89.94 billion by 2028, management fees - typically between 5% and 7% of gross income - are often outweighed by the benefits of streamlined operations, reduced costs, and expert guidance. As Sarah Stapley, Marketing Director at Crescendo Self Storage Management, puts it:
"Outsourcing can be a smart and cost-effective way to enhance your self-storage operation and achieve long-term business goals."
By leveraging storage facility solutions, owners can tap into a range of advantages, such as:
- Cutting-edge technology for inventory and facility monitoring
- Comprehensive staff training to elevate customer service
- Simplified maintenance and compliance management
- Smart pricing strategies to boost revenue
- Proactive risk management and emergency planning
To explore more ways to streamline your operations, check out our guide on third party self storage management.
These services, paired with the sector's rapid growth - over 252.3 million square feet of expansion in the last five years - highlight the importance of professional management. Our Turn Key Self Storage Facility Management service takes it a step further, offering a complete package that includes design, construction, and ongoing operational support. This all-in-one approach ensures facilities run efficiently, allowing owners to focus on driving their business forward.
FAQs
What are the benefits of outsourcing self-storage facility management instead of managing it in-house?
Outsourcing the management of self-storage facilities comes with a range of advantages that can make it a smart choice for businesses.
One major benefit is the ability to cut operational costs. By turning to experienced third-party providers, companies can avoid hefty investments in infrastructure, advanced technology, and hiring staff. This approach not only simplifies operations but also boosts efficiency, freeing up resources to focus on core business activities.
Another key advantage is the flexibility and scalability it offers. Businesses can adjust storage capacity to match changing demand without the burden of managing additional resources. Plus, working with industry experts ensures adherence to regulations and delivers a higher standard of service, which can enhance customer satisfaction and drive long-term growth.
How can outsourcing storage facility management reduce costs and boost profitability?
Outsourcing the management of storage facilities can be a smart move for businesses aiming to save money and boost profits. By bringing in professional management, companies can streamline their operations, making better use of resources while cutting down on labor costs. It also helps avoid common pitfalls like overstocking or running out of inventory, both of which can be expensive mistakes.
Working with third-party providers opens the door to shared warehousing options, where businesses only pay for the space and services they actually use. This kind of flexibility makes it easier to scale operations without the hefty fixed costs tied to running in-house facilities, which can have a positive impact on overall profitability.
How can I smoothly transition from managing my storage facility to outsourcing it?
To make the shift from managing your storage facility yourself to outsourcing as smooth as possible, start by assessing your current operations. Pinpoint areas like customer service, billing, or maintenance that could benefit from professional oversight. This step will clarify which responsibilities are best handed off.
The next step is to select a trusted third-party management provider with experience in the self-storage sector. Prioritise companies that offer customised solutions, understand your business objectives, and have a solid history of delivering results.
Lastly, establish clear expectations with your chosen provider. Outline performance goals, service standards, and reporting needs to ensure open communication and a productive, long-term partnership.
Related posts
- 7 Key Features of Modern Self-Storage Facility Design
- How Smart Design Impacts Storage Facility Profits
- How External Garage Units Maximise Space in your Self Storage Facility
Maximising Space with Partitioning Systems: A Practical Guide
Want to make the most out of your self-storage space? Here's how partitioning systems can help you maximise storage capacity, improve security, and reduce maintenance costs - all while creating a polished, professional look.
Key Takeaways:
- Efficient Use of Space: Adjustable panels and mezzanine structures help you utilise vertical space effectively.
- Durable Materials: High-tensile, corrosion-resistant steel ensures long-lasting performance.
- Enhanced Security: Multi-point locks and protective features like corner guards boost safety.
- Professional Appearance: High-gloss finishes and customisable designs create a clean, branded look.
- Lower Maintenance Costs: Corrosion-resistant materials and protective features reduce wear and tear.
Whether you’re building a new facility or upgrading an existing one, smart design, durable materials, and proper installation can transform your storage space into a secure and efficient facility. Ready to optimise your storage? Let’s dive in!
Basics of Self-Storage Partitioning
Core Components
Effective self-storage facilities rely on durable materials and smart design. The walls of each unit are typically constructed using corrosion-resistant, high-tensile steel panels. Most facilities use 500mm wide, high-gloss panels for corridors, combining strength with a polished look.
Here are the main components:
Component | Function | Key Features |
---|---|---|
Wall Panels | Separate storage units | High-gloss finish, corrosion-resistant |
Security Doors | Control access | Multi-point locks, customisable colors |
Mezzanine Structures | Maximise vertical space | Multi-level storage capabilities |
Protection Features | Extend system lifespan | Corner guards, kick plates |
These components not only divide storage spaces but also improve functionality, security, and overall usability.
Space and Security Benefits
Partitioning systems are designed to optimise space and enhance security. Adjustable panel heights allow you to make full use of vertical space, maximising storage capacity from floor to ceiling.
Some key advantages of a well-planned partitioning system include:
- Efficient Space Use and Security: Adjustable panels make the most of vertical space, while strong steel construction provides excellent protection.
- Lower Maintenance Costs: Corrosion-resistant materials reduce upkeep over time.
- Professional Look: High-gloss finishes create a clean, polished appearance.
Protective features, such as corner guards and kick plates, further increase durability and minimise wear and tear. For more tips on optimising space and ensuring security in your self-storage facility, check out our installation guidelines.
Divider Walls 5 minute Installation - For Containers Storage UK
Space Planning and Design
Effective space planning begins with identifying your facility's specific needs and opportunities. A well-thought-out partitioning system can transform unused areas into a profitable storage facility by optimising layout and making the most of available height. These planning steps work hand-in-hand with the durable partition systems discussed earlier, ensuring every square foot is put to good use.
Site Analysis
A detailed site analysis helps optimise your space while maintaining accessibility. Key considerations include corridor widths, unit sizes, door clearances, and floor load capacity for multi-level designs. For more information on evaluating your facility, check out our design services page. Once you have a clear understanding of your site's layout, the focus shifts to making the most of vertical space.
Height Utilisation
Making full use of vertical space can dramatically increase rentable square footage. For instance, Kangaroo Self Storage's three-floor design and Ready Steady Store's custom two-floor system showcase how vertical planning can expand capacity and profitability.
"Our team collaborates from consultation through design to deliver bespoke height solutions that enhance both performance and appearance."
When planning vertical layouts, consider factors like building height limits, structural support needs, access to upper levels, fire safety standards, and proper lighting and ventilation.
Multi-level configurations can provide impressive returns by utilising space more effectively. A great example is Datastor in Newcastle, where ground and first-floor storage solutions were implemented to maximise efficiency while ensuring customer convenience.
sbb-itb-55d1b84
Materials and Equipment Selection
Choosing the right materials and features for your storage facility is crucial for ensuring durability, security, and ease of use. Modern partitioning systems blend sturdy materials with practical designs to create storage spaces built to last.
Partition Materials
High-tensile steel is a key material in professional partitioning systems. These panels resist corrosion and offer long-lasting performance while maintaining a polished look. A high-gloss finish adds extra protection against everyday wear.
There are two main design styles to consider:
- High-gloss flat panels for a sleek and modern look
- Corrugated panels for added structural strength
Protection Features
Beyond durable materials, additional protective features can help extend the life of your storage system. These features are designed to minimise damage and reduce upkeep. Some common options include:
- Corner protections to guard against damage in high-traffic areas
- Kick plates to shield lower panels from impacts
Together, these elements reduce maintenance and keep your facility in top condition. For instance, Ready Steady Store in Stoke implemented a two-floor system that highlights the effectiveness of these protective features.
Customer Amenities
Incorporating functional and tailored design elements during the initial setup can save costs down the line. A great example is Datastor in Newcastle, where a full-build installation for both ground and first floors showcased the benefits of early planning.
Selecting the right materials and equipment is the backbone of a successful storage facility. When paired with protective features and well-thought-out designs, these choices create a secure, durable, and user-friendly space. Next, we’ll dive into the installation process to bring these elements together effectively.
Installation Guidelines
Installing a partitioning system requires careful planning and attention to detail to ensure stability and efficient use of space.
Measurement and Setup
Accurate measurements are the foundation of a successful installation. Start with a thorough site survey to gather exact dimensions and identify any challenges. Customise high-tensile steel panels to meet your facility's height requirements. Pay close attention to factors like floor-to-ceiling clearance, door frame dimensions, unit sizes, layout, and access points. Use precision tools to confirm proper alignment and avoid misfitting components.
Once measurements are finalised, focus on ensuring the system's structure is sturdy and reliable.
Structural Support
Reinforce the structure for long-term durability. Use high-tensile steel and corrosion-resistant materials to enhance strength and minimise wear. Add protective features like corner guards and kick plates to reduce damage over time. For more detailed design and installation tips, check out our complete design services. These steps not only extend the life of your system but also improve its functionality, making it a key part of a well-operating self-storage facility.
Conclusion
Using an effective partitioning system is key to getting the most out of your self-storage facility. Facilities across Europe have shown how professional partitioning can improve storage operations and make better use of available space.
Careful planning and choosing the right materials are essential for success. Our 500mm high-tensile, high-gloss panels offer both strength and a polished look. Plus, with adjustable height options, you can create secure and efficient spaces that align with your facility's branding. This method ensures every design choice contributes to better performance.
To make the most of your project, work with experienced professionals who understand your facility's unique needs. Reach out to our complete design services team to explore how we can help turn your storage space into a well-organised, high-performing facility.
5 Benefits of Locker Storage Units for Your Business
Locker storage units can help your business save space, cut costs, improve security, and create a safer workplace. They’re flexible, scalable, and designed to fit various business needs, from small retail shops to large warehouses. Here’s a quick breakdown of the key benefits:
- Maximise Space: Use vertical storage and modular layouts to optimise your space.
- Save Money: One-time investment reduces long-term storage costs.
- Improve Security: Advanced features like tamper-resistant locks, keycard access, and CCTV keep items safe.
- Easy to Expand: Add or reconfigure units as your business grows.
- Enhance Workplace Safety: Organised storage reduces hazards and keeps workspaces clear.
Locker storage systems are a smart solution for businesses aiming to stay efficient, secure, and organised. Ready to upgrade your storage? Let’s dive into the details.
Benefits of Using Self Storage for Your Small Business
1. Better Space Usage
Efficient use of space is a priority for any business, and locker storage units are a smart way to maximise vertical storage while keeping floor space clear. These systems turn unused wall areas into functional storage, increasing capacity without requiring additional square footage.
Modern storage lockers come with designs that can be tailored to fit your specific needs. Got narrow hallways, tricky corners, or high ceilings? No problem. PSL highlights this advantage:
"One of the key benefits of our self storage locker systems is their versatile and space-efficient design."
Here’s why these modular systems work so well:
- Vertical Storage: Units can be stacked from floor to ceiling, making use of previously unused space.
- Flexible Layouts: Systems can be arranged in different ways to fit your available area.
- Size Options: Mix and match unit sizes to handle a variety of storage requirements.
These features make it easier to plan layouts that work for your space. Want expert advice? Check out our design services for more help.
When setting up your locker system, keep these points in mind:
- Traffic Flow: Ensure users can move easily while keeping the layout efficient.
- Accessibility: Place frequently used lockers in the most convenient spots.
- Security: Position surveillance equipment to maintain safety without sacrificing space.
2. Lower Storage Expenses
Keeping storage costs under control is crucial for any business. Investing in a reliable locker storage system can help cut down expenses over time by reducing maintenance needs. Our sturdy locker units are built to last, requiring very little upkeep, and come with PSL's dedicated support.
Unlike traditional storage options that involve ongoing rental and logistics fees, our locker systems are a one-time investment designed to keep future costs low. Check out our finance options and explore the full range of locker storage units to find the right fit for your business.
sbb-itb-55d1b84
3. Strong Security Features
Modern locker storage units are designed with advanced security measures to keep stored items safe. Our locker storage units combine digital and physical protections to create a secure environment for your belongings.
- Access control systems: Keycard and biometric authentication ensure only authorised individuals can access the lockers, while creating a digital record of all entries.
- Integrated CCTV: Constant monitoring helps detect unusual activity, keeping a watchful eye on your assets at all times.
- Tamper-resistant locks and durable construction: Built to resist forced entry, these features provide an additional layer of protection.
These features work together to protect your items and give you confidence in their safety. For more details, check out our security solutions.
4. Easy to Expand
These systems are built with security and efficiency in mind, but they also make growing your storage capacity straightforward.
Modern locker storage units are designed to grow with your business. Our locker storage units offer flexible configurations to make the most of your available space.
One client shared their experience:
"PSL's efficient installation made their storage expansion seamless and minimally disruptive."
Here's what makes the expansion process simple:
- Modular Layouts: Add, reconfigure, or modify units as your needs evolve.
- Expert Installation: Our team takes care of everything, from planning to setup.
- Business Continuity: New units are installed with minimal disruption to daily operations.
For a tailored plan, work with our design consultation team. They’ll help you address key factors like customer flow, accessibility, and security, ensuring your storage solution supports both current demands and future growth.
5. Better Workplace Safety
Organised storage isn’t just about space and security - it plays a key role in creating a safer workplace. Our locker storage units help reduce hazards and establish clear storage practices.
Fewer Trip Hazards
Keeping walkways and work areas clear lowers the chances of trips and falls, helping to prevent workplace accidents.
Streamlined Access
Our storage solutions are designed for ease of use, featuring:
- Clear labeling and designated spaces for items
- Convenient, easy-to-reach compartments
- Wide aisles for smooth navigation
Additionally, through our workplace safety consultation, we help businesses implement storage systems that improve safety and efficiency. Here's how well-organised storage contributes to a safer environment:
Safety Aspect | Benefit |
---|---|
Clear Pathways | Reduces clutter and ensures safe access |
Better Accessibility | Avoids awkward lifting and overreaching |
Emergency Readiness | Makes safety tools easy to locate |
Improved Traffic Flow | Prevents congestion in busy areas |
Proper labeling ensures items are easy to find while facilitating quick responses during emergencies.
Improved Security
Strong locks keep hazardous materials secure. Our security systems prevent unauthorised access, offering added safety and peace of mind.
Organised Workspaces
A well-structured storage system keeps everything in its place, reducing the risk of unsafe temporary storage. This applies to items like:
- Personal protective gear
- Cleaning products
- Tools and equipment
- Critical documents
When employees know exactly where to store and retrieve items, the workplace becomes not only safer but also more efficient.
Conclusion
Locker storage units can reshape how businesses manage their operations by providing storage solutions designed for today’s workplace challenges. These systems help make better use of space, reduce costs, improve security, and create safer environments - making them a smart choice for businesses aiming to stay efficient and organised.
Here’s what professional storage systems bring to the table:
- Better Space Use: Convert underutilised areas into practical storage.
- Cost Savings: Cut down on the need for external storage facilities.
- Stronger Security: Keep valuable items and sensitive materials safe.
- Flexible Options: Adjust to the changing needs of your business.
- Improved Workplace Safety: Maintain an organised, hazard-free environment.
If upgrading your storage is on your agenda, partnering with experienced providers can make all the difference. Through our workplace safety consultation, we help businesses implement storage systems that align with their unique requirements.
As Mini Lager shared:
"PSL completed my Self Storage conversion. I am very happy with my finished facility. PSL were professional and efficient and it was a pleasure to deal with them. I would recommend PSL as fit out contractors for European storage facilities as nothing was a problem on site and they were extremely helpful throughout the whole job."
Our security solutions ensure your storage system balances space efficiency with the security and accessibility your business demands. Ready to take the next step? Evaluate your storage needs, explore customisation possibilities, and connect with our experts to create a storage system tailored to your business. Reach out to our team today!
Related posts
- 7 Key Features of Modern Self-Storage Facility Design
- Why Outsourcing Storage Facility Management Makes Sense
- Design Smarter Facilities with Modular Storage Partition Systems